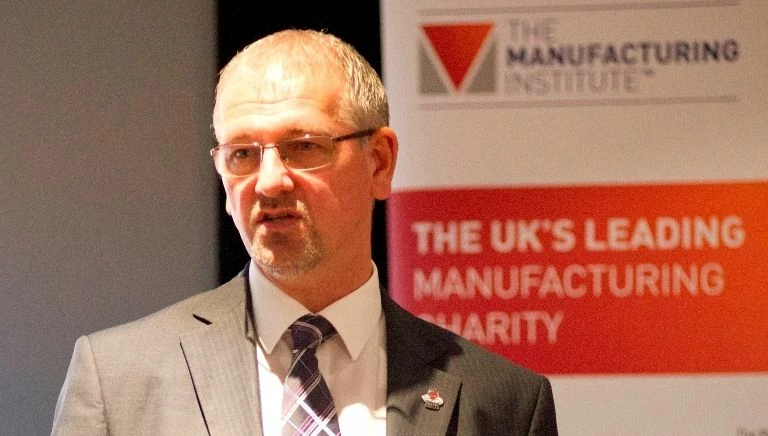
Partner Article
Discover what sets world-class manufacturers apart
A line-up of world-class sites has been announced by The Manufacturing Institute as part of the Shingo ‘Discover’ workshop series.
From eye care to engines and breakfast cereal to battery parts, this is an unrivalled opportunity to look behind the scenes at exceptional manufacturing sites to find out how they set themselves apart from the competition.
Delegates will spend two days on-site learning about the Shingo Model and its key principles, seeing first-hand why Shingo is the global standard for Operational Excellence. They will discover how to align and embed continuous improvement activities in their own organisations, sharing experiences with other like-minded professionals, all committed to achieving business excellence.
The Shingo ‘Discover’ workshops demonstrate how to transform business systems and culture, enabling delegates to see this in action and use their new-found knowledge to drive results and success.
Mike Price, Managing Director of The Manufacturing Institute, said: “As Europe’s first strategic partner for the Shingo Prize, The Manufacturing Institute has many years experience in leading enterprise excellence programmes and we are proud to have guided two companies towards achieving the ultimate Shingo Prize this year alone. Our managing consultants will share their authoritative knowledge and experience with delegates to increase their learning outcomes.”
Forthcoming dates and locations include:
29-30 April: Optos, Dunfermline A developer and manufacturer of medical devices and solutions for eye care professionals, Optos is global leader in retinal imaging technology, achieving ultra widefield, high resolution imagery unmatched by other devices. The company has used Shingo principles to help it double capacity and save £3 million.
14-15 May: Volvo, Venissieux (near Lyon) This plant – a former Renault facility – was acquired by Volvo in 2003 and manufactures six- and eight-litre engines for Volvo plants across the world. It has deployed – to great effect – the World Class Manufacturing system developed by Professor Yamashina.
4-5 June: Kellogg’s, Manchester The Manchester plant is the company’s largest cornflake producing plant and has been making world famous brands since 1938. Four years ago, it embarked on a lean transformation and has made significant improvements to its productivity, culture and safety.
18-19 June: Entek, Newcastle Entek makes battery separators in this high-volume, process manufacturing operation, and exports 100% of production. Entek has developed a strong culture, where people live and breathe continuous improvement and manufacturing excellence. An initiative to develop high-performance teams has led to a recently-announced £10 million investment at the site.
10-11 September: Post Danmark, Denmark With 15,000 employees and more than 700 outlets, Post Danmark is one of Denmark’s largest companies and is one of the best postal service providers within the EU. Quality checks are carried out continuously, based on the EFQM (European Foundation for Quality Management) model.
5-6 November: Ipsen, Wrexham Ipsen’s Biopharm factory employs 390 staff and began its lean transformation in 2006. The company has introduced a new leadership approach to effectively engage their wider team in continuous improvement across the site.
3-4 December PZ Cussons, Manchester PZ Cussons (UK) Ltd produces well known brands such as Imperial Leather, Carex, Original Source, Charles Worthington and Morning Fresh, exported globally. Its award-winning R&D and production site in Manchester has been redeveloped as part of a major modernisation of its wider supply chain - introducing significant automation and central measurement equipment.
Further information: www.manufacturinginstitute.co.uk/events or contact Carolyn Bayley on +44 (0)161 875 2525, carolyn.bayley@manufacturinginstitute.co.uk.
This was posted in Bdaily's Members' News section by The Manufacturing Institute .