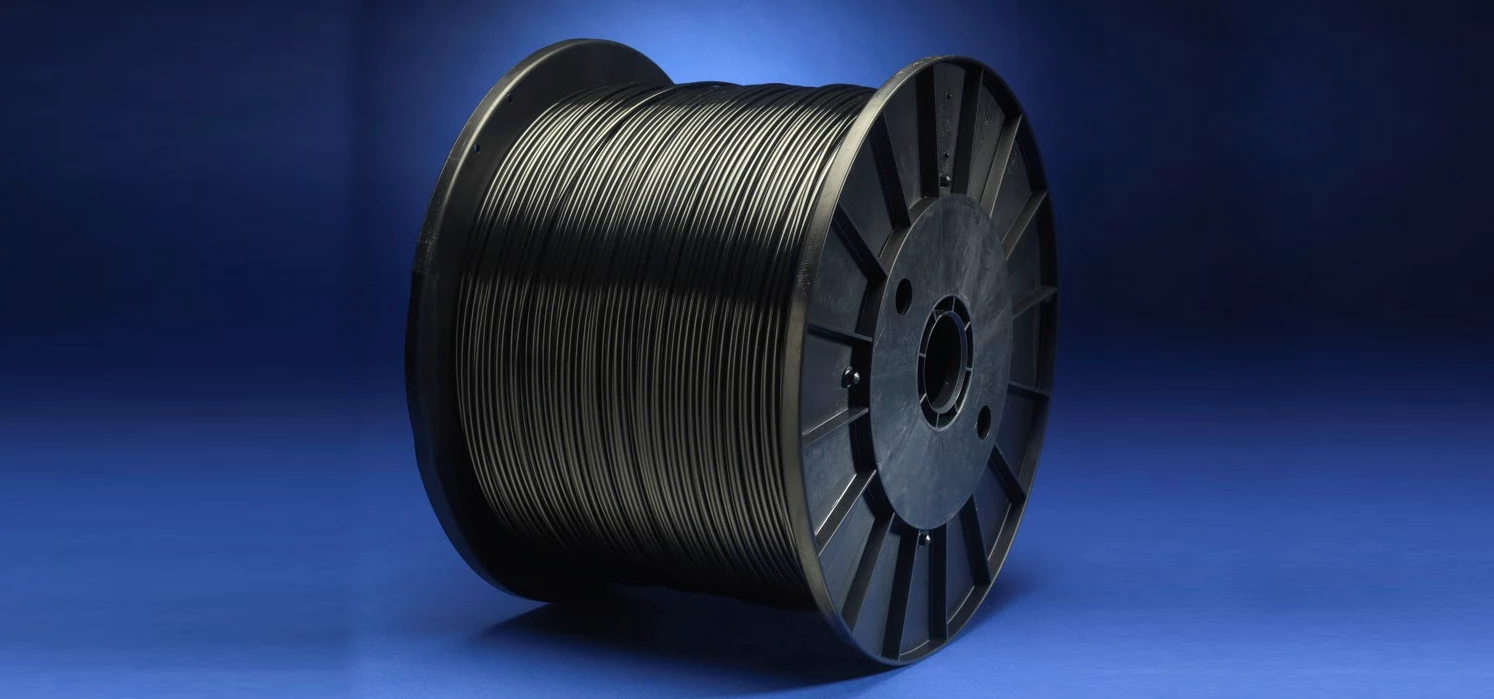
Partner Article
Sheffield manufacturing company develops green alternative steel wire
DR Baling has developed a green alternative to steel wire, which is set to save the waste industry tens of millions of pounds.
The Sheffield-based manufacturing company, which currently produces 1000 tons of steel wire a month, has innovated and diversified to future-proof the company and jobs of its 19-strong workforce.
The Yorkshire manufacturer is investing an ongoing £2.5m in developing PlasLOC, a heavy duty non-slip plastic wire which is set to take over the role of steel wire in the baling of waste.
The wire, which has the same properties as steel, can be incinerated during the waste process. It has the potential to save the waste industry tens of millions of pounds by simplifying the recycling process.
The innovative new product enables a cheaper and more environmental way to dispose of waste via incineration and will positively impact on the amount of waste going to landfill.
By 2016 the amount of biodegradable municipal waste sent to landfill must be reduced to 35% compared to 1995 levels. Waste companies also face a financial levy of £82 per tonne in Landfill Tax making the landfill option costly and prohibitive.
By switching to PlasLOC, waste companies are now able to fully incinerate baled waste within Mechanical Biological Treatment (MBT)plants. Until now, steel wire had to be removed from bales before incineration which significantly increased costs.
A quicker turnaround at MBT plants means more baled waste can now be recycled and turned into renewable electricity.
PlasLOC can be manufactured at 20% the cost of steel wire and since its launch in September it is being rolled out to DR Baling’s European customers. A launch into the American market is planned for 2016.
DR Baling managing director Peter Robinson, who privately funded the two-year R&D project, said PlasLOC was born out of a need to diversify in the face of cheap foreign imports.
“DR Baling has spent 50 years at the forefront of baling wire manufacture but it has become increasingly difficult to compete again subsidised foreign steel imports, notably from Spain.
“In order to secure the future of the business and safeguard jobs we innovated and the result is PlasLOC. I can see a day in the not too distant future when all our customers have switched from steel wire to PlasLOC.
“It has been a long journey to develop this product and ensuring the correct tensile. We’ve developed the plastic extrusion and downstream processes in-house and by applying expert knowledge we’ve developed a pioneering product with unique tensile, stretching, heating and coiling properties.”
This was posted in Bdaily's Members' News section by Ellen Forster .
Enjoy the read? Get Bdaily delivered.
Sign up to receive our popular Yorkshire & The Humber morning email for free.