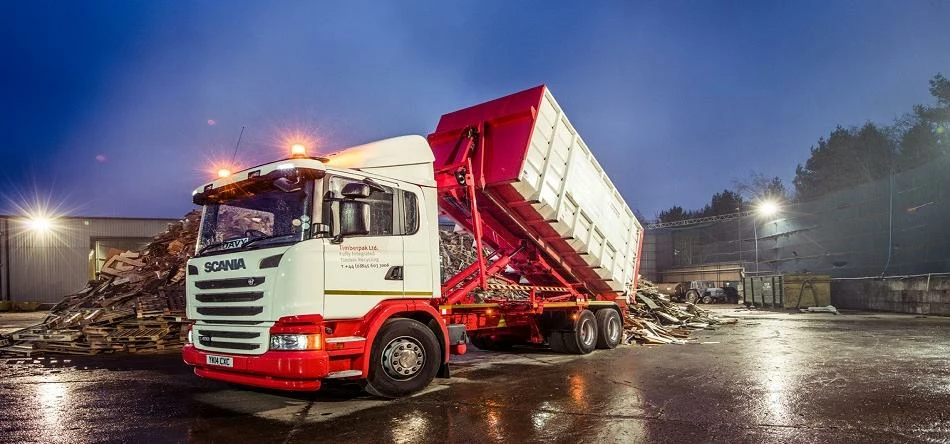
Behind the Business with Egger UK
Bdaily goes behind the business with Mark Hayton who is Director at Timberpak, the wood waste sourcing and processing firm who have centres in Leeds, Washington and Glasgow.
Can you give a synopsis of your area of expertise?
My background is in wood-based materials manufacturing starting back in 1989. Since 2003 I have worked for EGGER and I am responsible for the recycled wood requirement for the two EGGER UK production facilities.
Can you give a synopsis of what your organisation does?
Timberpak is a wholly owned subsidiary of one of Europe’s largest wood-based materials manufacturers, EGGER. We are responsible for sourcing, sorting, cleaning and processing various forms of wood waste.
As part of this we are able to offer a guarantee that is twofold. Firstly, all acceptable material will be 100% recycled and used in the production of chipboard panels at our parent company’s production sites in the UK. Secondly, as we are the end user we are able to guarantee to offer consistency in our acceptance of acceptable materials.
We are a dynamic and fast growing company, now in its 15th year as a Timber Waste Management Company. We operate from three fully waste licensed recycling centres which are spread across the northern part of the country, at Cross Green Industrial Park in Leeds; Pattinson Industrial Estate in Washington, Tyne and Wear and Bellshill Industrial Estate, Bellshill, Glasgow. Timberpak are proud to be accredited to ISO standards 9001, 14001 and 18001.
Timberpak operates a system which provides flexibility for its customers by offering two services:
1. Material acceptance: For those customers who wish to bring their own wood waste to our sites.
2. Collection service: We offer a flexible collection service using specialist hook loader vehicles to collect roll-on, roll-off bins measuring 40 cubic yards from our customer sites as well as the option of collection via specialist waste ejector vehicles operating out of our Bellshill depot for our Scottish customers.
What key challenges has your company recently faced?
The main challenge we meet on a daily basis is the quality of waste wood. At Timberpak we are able to offer a 100% recycling route for waste wood as this wood is processed, cleaned and processed again for inclusion into the wood-based material products manufactured by the two UK EGGER plants.
The one product that is in the wood stream more than anything else is MDF. Unfortunately MDF cannot be recycled due to its makeup. If this gets into our waste wood stream when it is processed it fiberizes, causing blockages and screen issues in the main plant. We therefore work very hard to educate our suppliers to try to educate them about removing the MDF first.
What is your biggest achievement over the past 12 months?
The biggest achievement is by far and away the total volume of wood we handle and can proudly say we recycle. In our last financial year across our three sites we handled a combined inbound and outbound total of 51,000 vehicles. This equates to 202 loads per day, which were carrying a total of 533,000 tons of waste wood or 2,115 tons per day. This is the equivalent to 2.9 vehicles or 3.53 tons of wood each and every operational minute.
What is your most important focus for the coming year, and what do you hope to achieve?
Our focus is to work with our “Partners” on Quality. We call our suppliers Partners as we feel they are more than suppliers. We want to further educate them about what can and what cannot be recycled, in order for them to maximise their own wood waste into the most efficient use. We hope to offer the most cost effective outlet for waste, being the end user.
What excites you most about your industry and business?
The changeability of it, the waste wood market is seasonal, busy in the summer and quieter in the winter. However our demand is constant, so getting the balance right is crucial, and managing this balance under the constraints put on our industry by our licence is challenging.
What do you wish you’d known when starting out?
Exactly how the business would have developed. We started 16 years ago in 2000 in Leeds on a leased site handling between 10 and 20 thousand tons per year, that site now receives 100,000 tons and we have outgrown it. We now need to find a larger more suitable site in order to grow further. If we had realised this we would have invested initially in a larger bespoke site, but back in 2000 we didn’t see exactly how the recycled wood market was going to develop.
What will be the “next big thing“ in your industry, and how do you plan to handle it?
The next big thing in our industry is already here, it is FPP or Fire Prevention Protocol. This is a guidance document introduced by the Environment Agency to try to reduce the amount of fires that occur each year in the waste industry.
This is not something that happens very often in waste wood facilities. However, it is seen more frequently in general waste recycling businesses. However the constraints under the current guise of this policy are inflexible and un workable. It is truly a challenge under FPP to be able to still offer the most cost effective route for our Partners’ wood waste but still provide a service and supply the two EGGER plants with the required raw materials.
We see the recycling of wood as essential and it has enormous environmental benefits.
Looking to promote your product/service to SME businesses in your region? Find out how Bdaily can help →
Enjoy the read? Get Bdaily delivered.
Sign up to receive our popular Yorkshire & The Humber morning email for free.