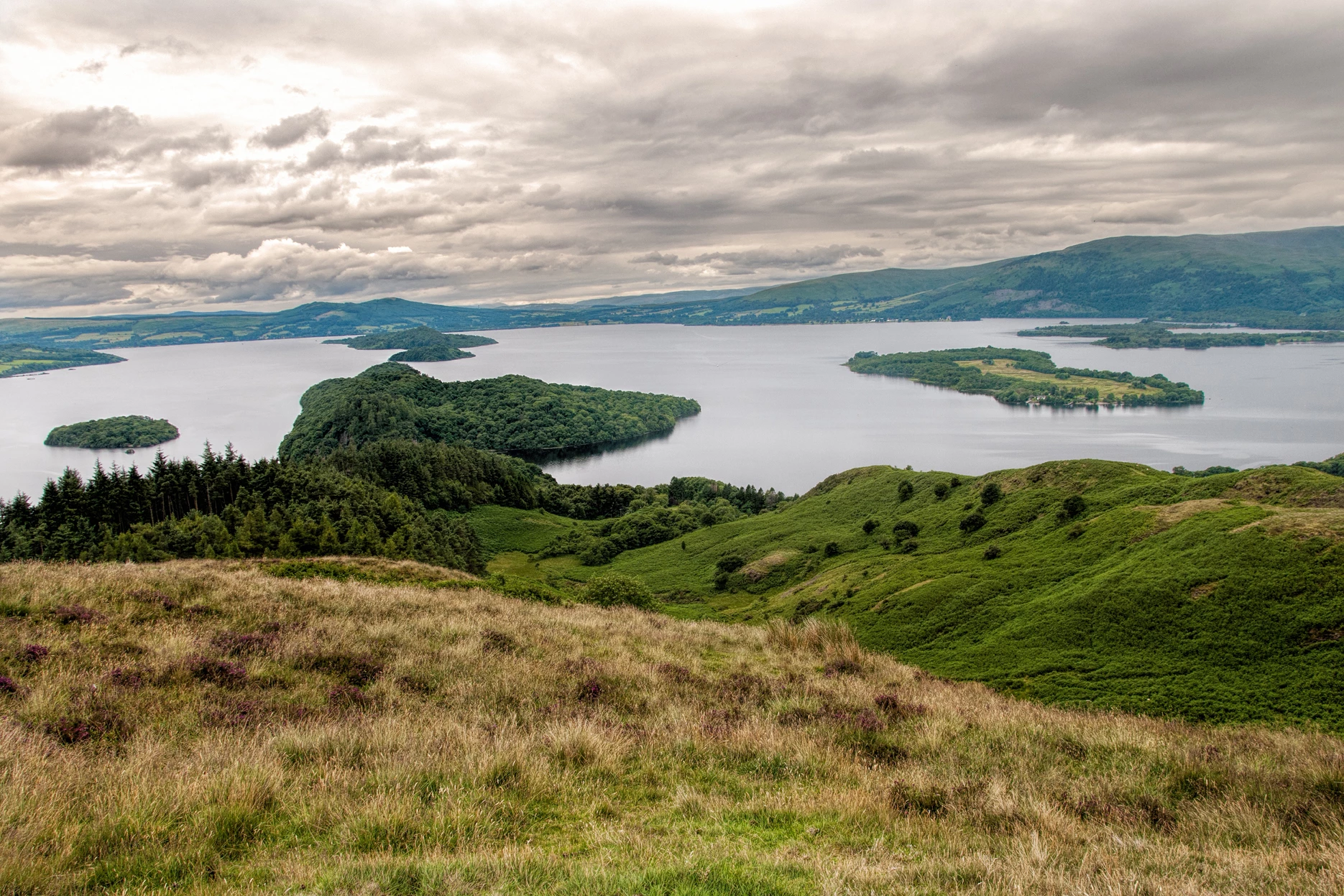
Durham software firm collaborates with Scottish whisky group on its latest project
Scotland’s Loch Lomond Group - a company behind various artisan whisky brands - has appointed Indigo Software to implement Indigo WMS warehouse management software and more efficiently manage sales order processing within five of its bonded warehouses.
Durham’s Indigo will commence the project to transform Loch Lomond’s paper-based warehouse processes with real-time warehouse management in May 2018.
Founded in 1814, Loch Lomond Whiskies can trace its roots back to the Littlemill distillery. It was established in 1772 and is thought to be one of the oldest in the world.
Its current malt and grain distilleries, in Alexandria, Dunbartonshire on the banks of Loch Lomond, were built in the 1960s and are among only a few in the industry to maintain an onsite cooperage.
The malt distillery at Alexandria also features a unique combination of traditional swan neck and distinctive straight-necked pot stills, enabling it to produce a diverse range of flavour profiles.
After experiencing a phase of sustained business growth and investment, following the company’s acquisition in 2014 by private equity group, Exponent, Loch Lomond has transformed the scale of its business.
Over the past few years, the product range has quadrupled in size and the company now stocks over 850 different SKUs of product varieties, which are shipped globally. This represents a huge shift from its commercial position just a few years earlier.
Export markets have now grown tenfold and over 250 pallets of finished goods leave the Ayrshire site each day, for onwards distribution to customers.
Loch Lomond Group’s investment in Indigo WMS is seen an essential part of the company’s transition to become a leading global whisky producer.
Implementing a warehouse management system will allow the company to automate the management of incoming raw materials and finished goods, plus improve sales order processing.
Tony Brewerton, Plant Director at Loch Lomond Group, said: “Our growth means we have effectively outgrown the original processes that served us so well for many years.
“It’s a good problem to have because it demonstrates how we have progressed our brand visibility and volume.
“Implementing Indigo WMS will allow us to make finished goods put away much more efficient and ensure we are achieving a higher proportion of ‘on time in full’ (OTIF) shipped pallets, which is critical for customer satisfaction.”
Traceability is another important consideration for Loch Lomond, to maintain accurate product records and guard against counterfeited goods. Each bottle produced has a unique lot code identifier denoting the line, date and time of production.
Indigo WMS is supporting this process by capturing lot code information at the goods inwards stage and tracing it right through to the end customer. This enables Loch Lomond to verify product authenticity and demonstrate that the duty has been paid.
Once implemented, Indigo WMS will also be integrated with Loch Lomond’s JD Edwards ERP solution.
Eric Carter, solutions architect at Indigo Software, concluded: “We frequently encounter situations where an artisan food and drinks manufacturer is migrating from paper based systems and introducing a WMS as their first level of automation.
“In these cases, adding wi-fi into a legacy site can be very expensive and it’s not always a necessity as this project demonstrates.”
Looking to promote your product/service to SME businesses in your region? Find out how Bdaily can help →
Enjoy the read? Get Bdaily delivered.
Sign up to receive our daily bulletin, sent to your inbox, for free.