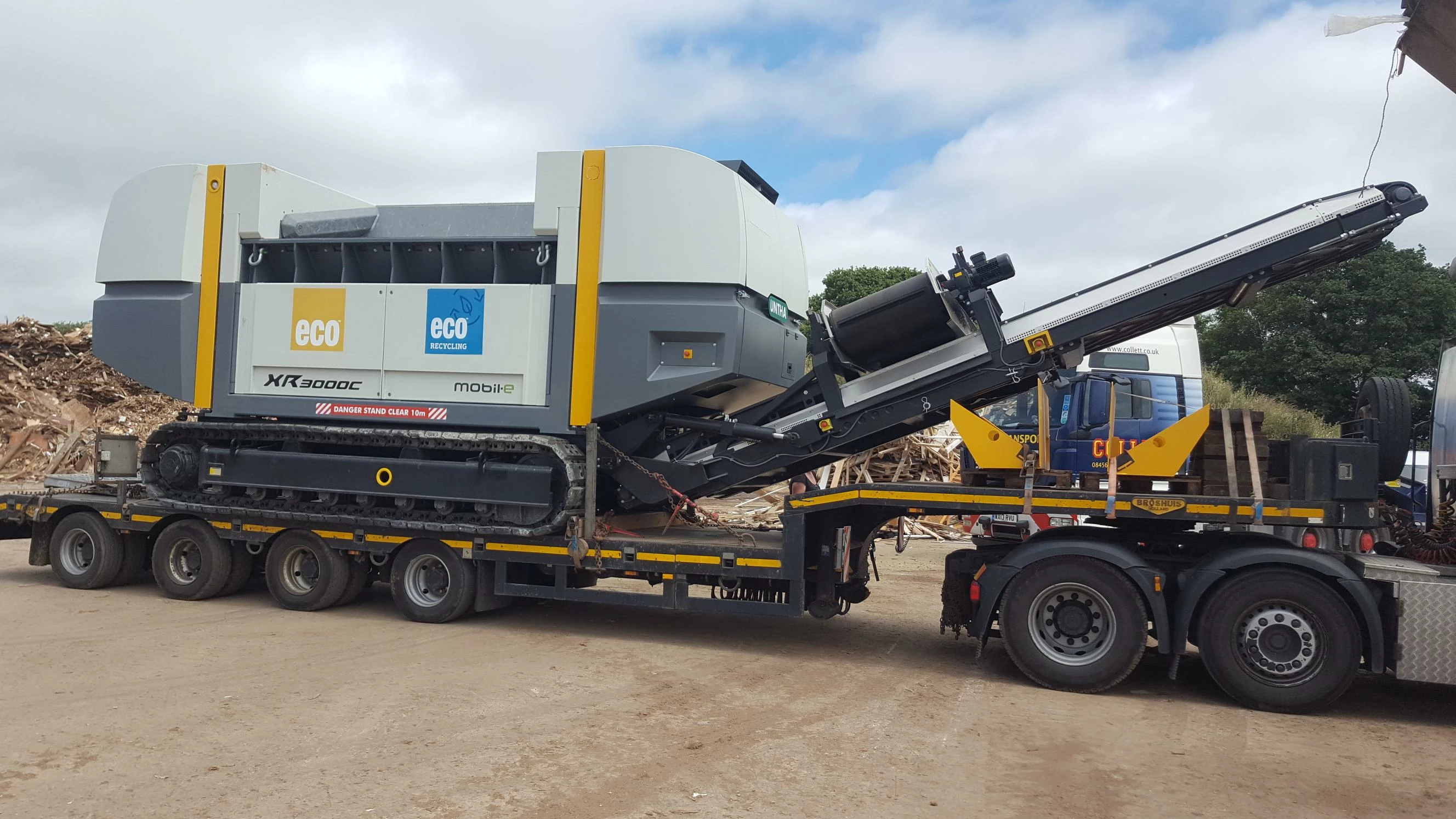
Partner Article
Shredding investment decarbonises pioneering biomass operation
Organics recycling and renewable energy expert Eco Sustainable Solutions has overhauled its biomass shredding technology to decarbonise the organisation’s approach to alternative fuel production.
Converting over 300,000 tonnes of waste into saleable products per annum, the business is no stranger to the energy market. But having recently installed a new combined heat and power (CHP) plant to harness the value of the fuels from its Parley facility, the goal was to improve the net environmental gain of the closed loop operation.
Eco has therefore invested in the highest specification mobile UNTHA XR3000C unit, with 2 x 132kW drives. The shredder can process Grade C wood waste to produce a P63 specification biomass fuel in a single step, at a rate of 25tph, or a pre-break output at 40tph.
With a hard-faced rotor, quick-change screen, wide sweep ram and specialist biomass cutting system, the machine will also achieve a low wear rate to minimise whole life costs. But of particular interest in a market dominated by diesel shredders, was the XR’s electric drive, which has hit the headlines over the past 18 months for its ability to reduce clients’ energy consumption by up to 50%.
Eco Sustainable Solutions’ operations director Justin Dampney explained: “Because we can self-power the machine using our own electricity generation, we are further closing the loop of our waste to energy business operations.
“But the story doesn’t end there. We’re currently exporting our biomass product, but it will soon be used as fuel within a large scale domestic green energy plant. If we’re going to the effort of manufacturing a renewable energy source, it is important that we maximise the environmental and commercial benefits stemming from the process.”
Eco’s first trial of the XR was more than two years ago, and such is the magnitude of the investment, that extensive due diligence has continued in recent times to verify the throughputs and homogenous quality of the output product.
A visit to IFAT in Munich this May concluded the procurement process. Despite UNTHA offering a number of finance packages, Eco decided to purchase the XR mobil-e outright in addition to a service and maintenance contract, plus critical wear parts package.
Justin concluded: “This is traditionally an energy-hungry sector, with noisy, high wear and high maintenance equipment. But as we prepare to upscale our renewables agenda, it is important that we have the most cost- and environmentally-efficient technology in place to support our operations.
“We were impressed by not only this machine, but also the performance commitment and professional service of the UNTHA team. We’re looking forward to putting the shredder through its paces as our business evolves.”
This was posted in Bdaily's Members' News section by Katie Mallinson .
Enjoy the read? Get Bdaily delivered.
Sign up to receive our popular Yorkshire & The Humber morning email for free.