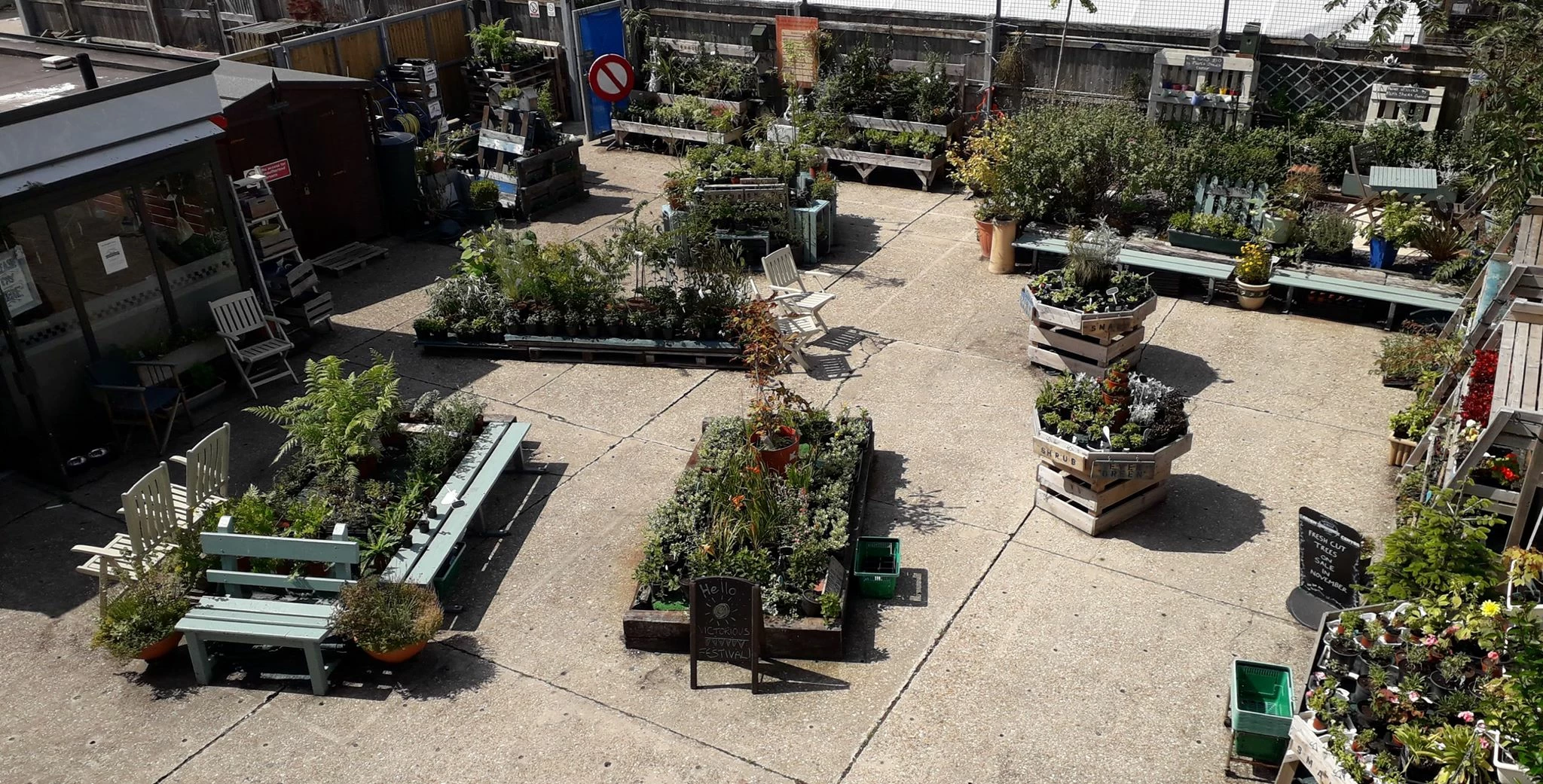
Partner Article
Lean Skills help those with Learning Disabilities
Lean training skills are being used to help individuals with learning disabilities become more independent with the ultimate aim of finding work, specifically in the horticulture and agriculture industries.
Catherine Burland, who works for the Parks Service of Portsmouth City Council, had been trained in Lean by Gosport-based Lean business specialists Fedden USP, in her previous role working for a commercial garden nursery. She realised that Lean tools have the potential to benefit those with memory issues, including brain injury and dementia, those with learning disabilities, Sensory Processing and Learning Difficulties (SPLD) and autism, which can be heavily reliant on structure and routine.
Catherine is now running a Portsmouth City Council project at the Waterfront Garden Centre in Portsmouth, where Lean methods are applied to support small groups of eight or nine adults with a variety of learning disabilities. In addition, she has 15 volunteers to help her with the training to enable individuals to attain a standard comparable to a Level 1 NVQ in Horticultural Skills.
Standard operations where both pictures and words are used to document in detail a particular process, is one of the Lean tools that is being used with the groups. Visual management is also very helpful, such as labelling storage so that individuals can see what is in a cupboard before opening it; this enables individuals to have greater independence and autonomy to begin and complete tasks.
Catherine said: “The application of Lean learning processes has gone a long way to helping our supported individuals and our volunteers, all with differing needs and abilities, to gain improved skills to help them become more employable and confident in their daily lives. And it helps with a large age group as we support individuals ranging from 18 up to their mid-60s to achieve their own personal goals.”
SMART goals are used and supported individuals have user-led action plans to identify what they are hoping to achieve from the programme, such as improving social abilities or becoming more employable; it can be different for each of them.
Neil Fedden, owner and Managing Consultant at Fedden USP, said: “Both standardisation and visual management are the key Lean tools that can help individuals with learning disabilities. The standardisation provides a clearly defined process that is both repeatable and well documented and the visual management aspect puts more focus on communicating how the process operates through pictures and colour rather than just relying on written or verbal communications. It’s good to see how Lean can be used in this way.”
This was posted in Bdaily's Members' News section by Colin Bridgman .
Enjoy the read? Get Bdaily delivered.
Sign up to receive our popular morning National email for free.