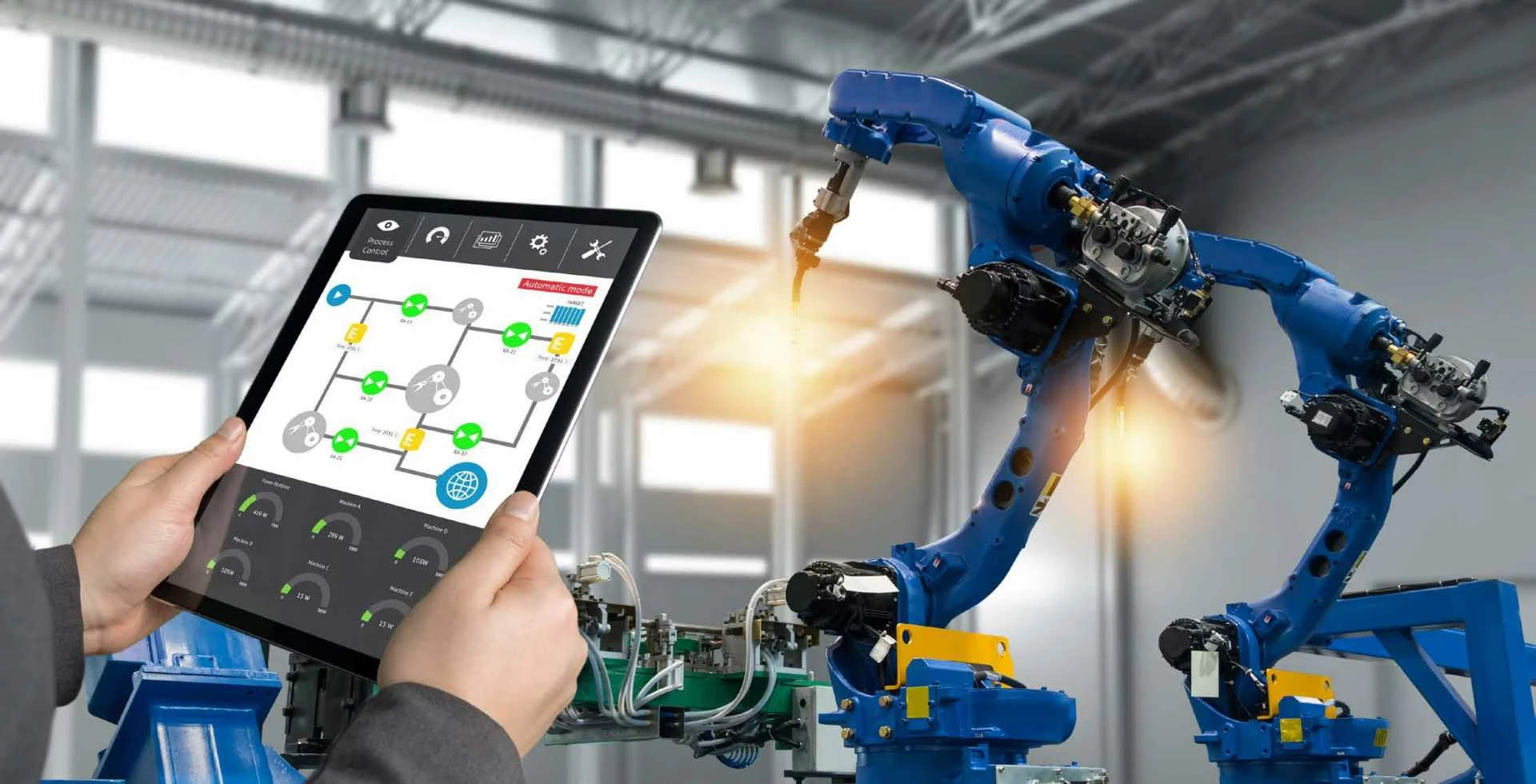
Partner Article
The need for speed: Why the success of Industrial IoT will rely almost entirely on connectivity
From its earliest times, manufacturing has always been at the forefront of automation and transformation. As the fourth industrial revolution (4IR) continues to drive unprecedented change and positive disruption across the manufacturing sector, one of the driving forces behind this change and disruption is the rapid growth in deployments of Industrial Internet of Things (IIoT) solutions.
Intelligent, connected monitoring devices, robotics and data-led decision making have been implemented across production lines for some time now, but that’s set to increase dramatically, enabling a far greater amount of accessible data, at greater speeds and ever more efficiently. Figures from IDC estimate that more than £575bn will have been spent on IoT systems and services globally in 2019, including an estimated £59bn on manufacturing operations. Analysts also predict the quantity of installed IIoT devices such as robots and sensors to jump from £237m in 2015 to £923m by 2020, totalling roughly £205bn in spending over the five-year period.
The number of connected devices and quantity of data being processed on the factory floor will bring new connectivity challenges. A robust and reliable network infrastructure is crucial to manufacturers realising the benefits of IIoT, such as cost savings due to predictive maintenance, improved safety, and other operational efficiencies. IIoT networks also allow industrial organisations to break open data silos and connect all of their people, data, and processes from the factory floor to the executive offices into one digital ecosystem. An example of this type of solution can be found in Ocado’s automated warehouse, where robots are able to pick and sort an order in a matter of minutes, processing the 3.5m items that go into their 65,000 orders each week.
Connectivity to drive growth
As this adoption of IIoT accelerates rapidly across the industry, 2020 will be the year that manufacturers increase their investments in connectivity infrastructure to support growth ambitions and provide sustainability. The watch word of next generation 4IR manufacturing is ‘integration’– of systems, people and processes. For things to be integrated, they have to be connected, and so by definition, integration means that connectivity must sit at the heart of this new stage of digital transformation.
Whether it’s IIoT, AI, robotics or machine learning, low latency connectivity is a huge priority for IT and operations leaders in manufacturing. Likewise, capacity is critical. As more devices and more users connect to more systems, the dataflows quickly become mindboggling and the bandwidth needed to carry this data is ever greater. This is even more true when the transformative capabilities that 5G will bring are considered. What’s more, as today’s manufacturing methods have an increasingly global footprint, managing the flow of materials and processes across multiple locations is the norm – so network visibility and availability is vital.
Today, many manufacturers are addressing these challenges by taking advantage of SD-WAN services, working alongside their existing network solutions. SD-WAN provides the advanced connectivity manufacturers need, giving enhanced levels of network visibility, flexibility and scalability. This allows for more dynamic management of new end-points, as well as actively prioritising the management of critical IoT devices in order to ensure the best possible network routing. SD-WAN also delivers the superior performance, reliability and security needed to dynamically define the optimised network configuration for emerging technologies that will drive the next wave of transformation.
Investing in today for the benefit of tomorrow
Manufacturing and its supply chain account for more than three million jobs in the UK and the productivity of the sector is intertwined with the future prosperity of the UK. However, without the high-speed, high-quality connectivity that makes smart devices, data-informed processes and human/machine interactions possible, ambitions for the sector may not be met.
IT leaders in manufacturing organisations find themselves at a unique juncture, with the opportunity to influence the development of the sector like never before. The need for speed is here, and those who grasp the opportunity have the chance to shape manufacturing as 4IR develops. It’s time to seize the moment and enjoy all of the benefits the 4IR has to offer.
This was posted in Bdaily's Members' News section by Jonathan Rowan .
Enjoy the read? Get Bdaily delivered.
Sign up to receive our popular morning National email for free.