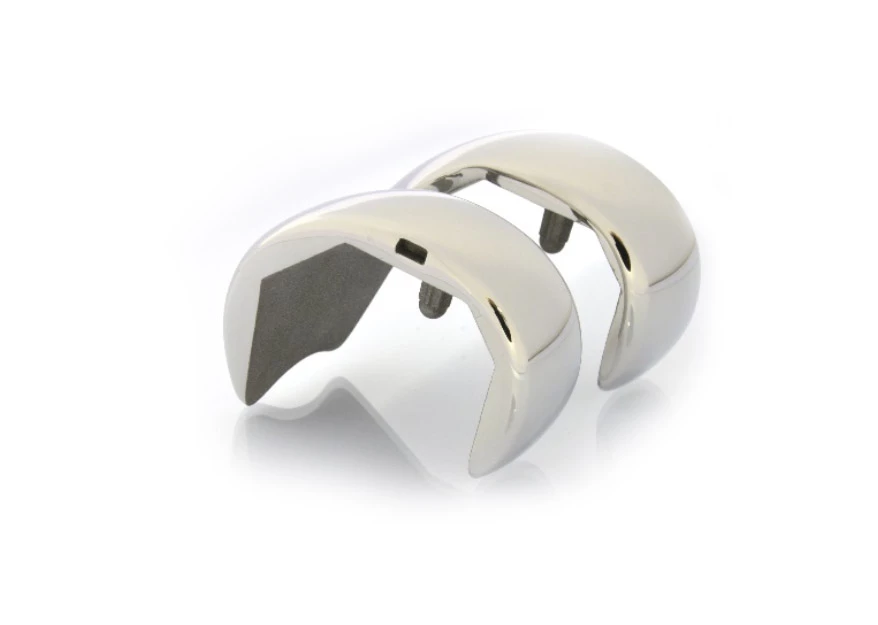
Partner Article
Protolabs launches new 3D printed cobalt chrome
The UK’s fastest digital manufacturer has launched 3D printed cobalt chrome - a new material from Protolabs - resistant to heat, wear and corrosion for use across multiple sectors.
The super alloy could see the oil and gas industry able to design and develop cobalt chrome parts not previously possible, with the aerospace sector also set to benefit thanks to cobalt chrome’s high strength to weight ratio.
Andrea Landoni, 3D printing product manager for Protolabs, says: “Cobalt chrome is one of the toughest materials known and can be polished to an extremely smooth surface. The advantage of 3D printing it is that we can produce any shape that you want, whether it is for an unusual geometry or to save weight.”
Hard-wearing cobalt chrome is well known for its excellent corrosion and creep resistance. It can withstand temperatures of up to 600oC and its low nickel content gives it excellent biocompatibility making it ideal for orthopaedic and dental applications.
The 3D printing process used by Protolabs, direct metal laser sintering (DMLS), can produce very fine resolution parts down to a minimum feature size of 1.00mm with a minimum wall thickness also of 1.00mm.
DMLS uses a computer-controlled, high power laser beam to melt and fuse layers of the metallic powder together. The company can produce parts using the process in as little as a day, which they claim makes them the fastest digital manufacturing company in the world.
Landoni adds: “One of the problems of cobalt chrome is that it is so hard wearing that it is very difficult to produce parts from it using other processes such as CNC machining. The properties of parts produced by DMLS are also equal to or better than those of wrought materials and the process is ideal when the geometry or structure of a part is simply not possible using any other process.
“3D printing is also ideal for rapid prototyping if you need to test a new part for both form and function. The production process is rapid, from uploading the design into our Protoquotes software you will typically get a quote back within a few hours. Once approved, the part can then be produced for shipping in as little as a day. When you contrast this to the several days or even weeks quoted by other suppliers, then you can dramatically shorten your development and product lead times.”
For more information, please visit www.protolabs.co.uk.
This was posted in Bdaily's Members' News section by Russ Cockburn .
Enjoy the read? Get Bdaily delivered.
Sign up to receive our popular morning National email for free.