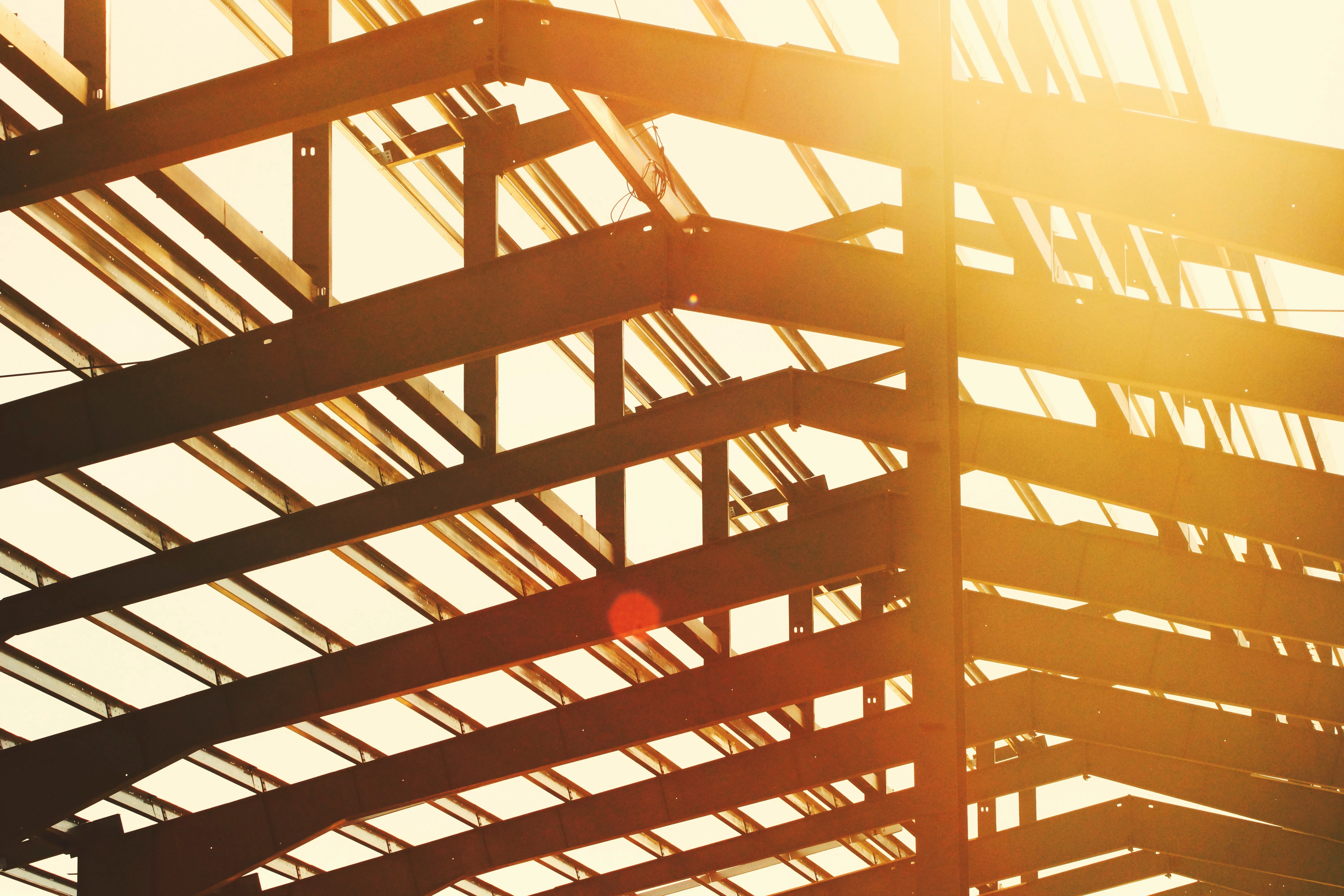
Partner Article
Modern methods of construction can catapult the UK towards its net-zero target
By Owen Evans, Managing Surveyor at Rund Partnership Limited
Modern methods of construction (MMC) has long been hailed as the answer to our housing crisis, by improving construction productivity in housing delivery using offsite and modular building techniques. Despite this, current use of MMC is still relatively low, and whilst the benefits associated with these methods are becoming more popular, one of the more pressing matters across the sector, is the need to adopt more eco-friendly construction solutions.
We’ve recently seen an escalation in forward-thinking developers incorporating more sustainable measures into their designs, plans and processes. However, with the UK Green Building Council reporting that 40% of all UK carbon emissions originate from the built environment, and with the government’s pledge to cut the UK’s emissions by 78% compared with 1990 levels by 2035 – the clock for change is ticking, from a sector strained by the pressures of demand versus supply.
MMC however offers a more sustainable way to build, and has the power and potential to be the golden thread of hope in ensuring the sector reduces its carbon emissions, but also in helping to address the housing shortage that has plagued the residential property sector for far too long. A problem that has concerned the sector in recent years, is the speed at which residential developments are reaching completion. Delays on site have often been a blight to project delivery times. A further issue has been the UK skills shortage, time and time again the skills shortage has been quoted as a contributing factor to poor quality homes.
However, in the wake of Covid-19, projects using MMC techniques demonstrated the benefits of its operating model. Whilst many sites paused their operations due to social distancing complications, projects utilising MMC were primed to keep operating throughout lockdowns, as sites required fewer workers and therefore were able to abide by social distancing measures. In addition, MMC techniques provide solutions to questions over new-build quality. The standardisation or precision-engineering of modular/offsite homes produced in a controlled factory environment, offers reassurances of high-quality finishes. These two factors are important improvements for the housing sector – however the positive contributions MMC can make to the UK’s sustainability agenda are too important to ignore.
MMC techniques are proven to significantly reduce waste generation on sites throughout the construction process. A recent study conducted by sustainability-focused charity Wrap, found that the construction industry produces 100 million tonnes of waste, which accounts for over a third of the UK’s total yearly waste. This is a high number that needs to be addressed by looking at each stage of a building’s lifecycle and identifying opportunities to eradicate waste and to ensure that the construction industry is making contributions that are more positive to the environment.
MMC techniques could help with this; by producing structural components in a factory and ensuring developers can work to precise amounts of materials, calculating to actualities rather than approximations.
Factory-built prefabricated homes can also help to reduce energy use through mass-scale manufacturing throughout the construction process. Beyond the construction phase, homes built using MMC techniques, are known to have lower energy consumption. Some modular construction uses innovative design and high-thermal conductivity materials comparative to traditionally built homes – meaning energy savings with longevity.
Further sustainable benefits include reducing emissions through the transportation and imports of building materials – and fewer people travelling to site.
For the UK, and the built environment in particular, achieving net-zero targets may be challenging without the use of MMC design and construction techniques. These techniques need to be considered and implemented at the very beginning of a project lifecycle, and then thoughtfully applied to the project throughout, taking into account the products that will have a positive effect on the environment over time – and not just for now.
This was posted in Bdaily's Members' News section by Teresa Cole .
Enjoy the read? Get Bdaily delivered.
Sign up to receive our popular morning National email for free.