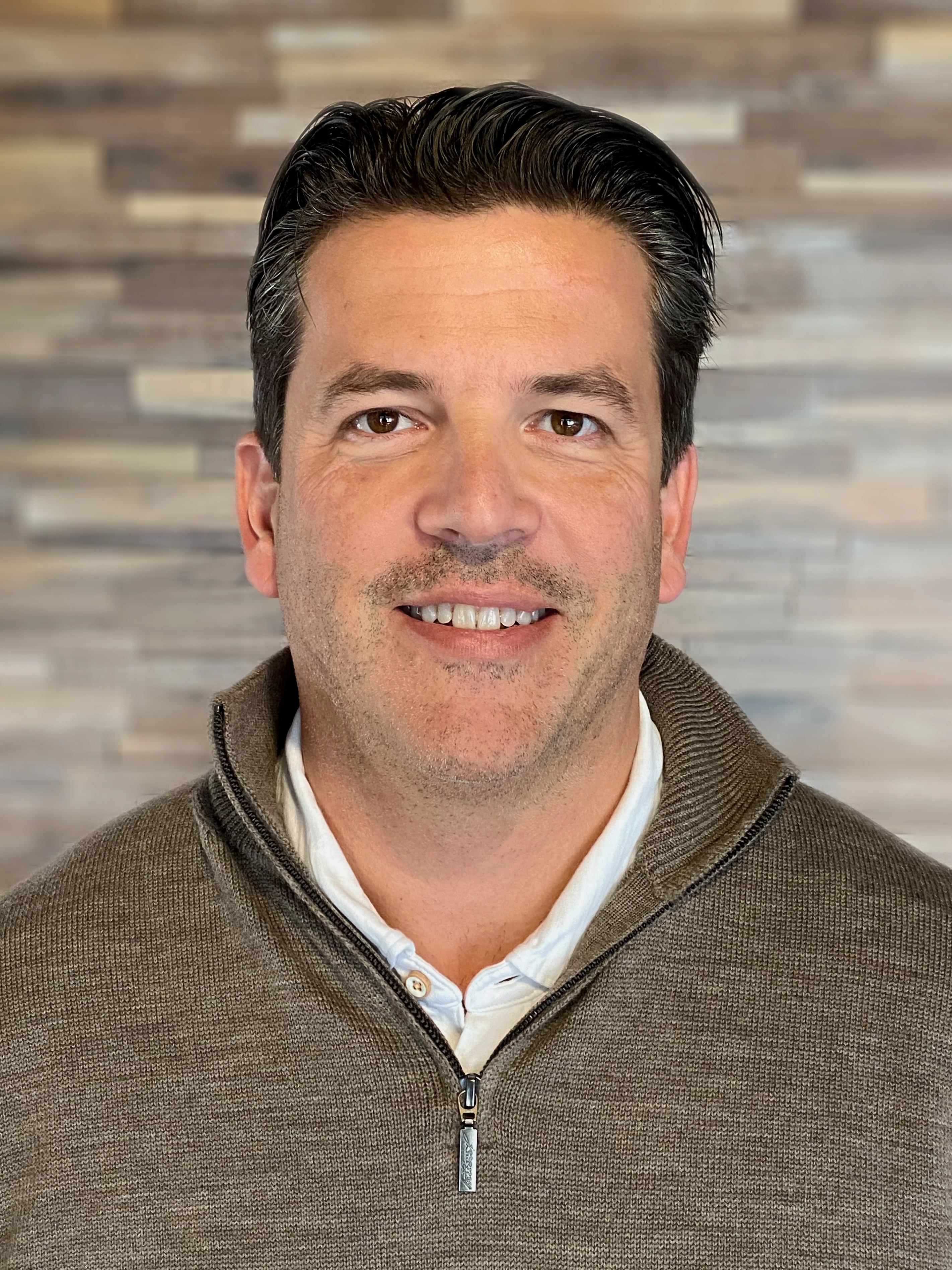
Partner Article
Fighting back against the growing manufacturing skills gap
The scale and severity of the manufacturing skills gap affecting developed countries such as the US and UK is no secret, and the pandemic has only made it worse. In the UK, a group of 20 MPs recently signed a motion calling for the Government to put manufacturing-centric skills at the heart of the National Curriculum to close a deficit that will require 186,000 skilled individuals to be hired every year until 2024 .
Meanwhile, in March’s budget, the UK Government laid out plans to reform technical education, improve apprenticeship schemes for employers and provide companies with incentives to employ apprentices, among other measures too , such is the extent of the skills gap currently faced by the UK. But while Government action is a welcome sight, the industry itself must also act now to solve the issue before the crisis deepens.
The pandemic’s hit us hard
The pandemic has only intensified these pressures, impacting the workforce and hindering productivity, with remote work becoming part of business operations for the first time. Baby Boomers have increasingly either chosen to take early retirement or have been forced into it due to their health, which has exasperated the situation. Of course, their know-how and experience are difficult to replace – especially amid the current working conditions. We’re now facing a perfect storm, where UK manufacturing is experiencing its largest skill shortage in 30 years .
Companies are scratching their heads as to how best to deal with the shortage, often adopting short-term fixes to cope as best they can. Due to retirement, redundancies, and furlough, among other reasons, many manufacturing companies have been left with no option but to deploy their workers across many departments. This creates a problem though; the staff members being asked to redeploy don’t always have the necessary skills or experience to fulfil the job roles they are suddenly being asked to do. This is resulting in a stretched workforce that does not possess the required expertise to ensure a company is operating at an optimum level and is keeping up with customer demand, as well as leaving other roles unfilled.
Rather than waiting for new blood, which is failing to come through, we as a manufacturing industry need to act now and use technology to strengthen, complement and enable the workforce we do have, increasing their capacity and capability to fit. A technological revolution is required which can, and must, solve this problem once and for all.
**The technical transformation opportunity **
Technology is ultimately the key to plugging the skills gap. Manufacturers need to embrace all aspects of digital transformation so remote workers can be better connected and troubleshoot more effectively while working remotely. Automating manual processes and eliminating paper on the plant floor will also boost productivity so plant floors can keep pace with supply chain demand. Cloud services, AI, automation, mobile process auditing software and enhanced cybersecurity measures are just some of the key technological advancements that must be invested in for factory processes to become fully digitized - thus greatly improving plant floor efficiency.
Dubbed the fourth industrial revolution, Industry 4.0 centres on connected cyber-physical manufacturing systems that leverage advanced technologies like artificial intelligence (AI), cloud computing and the internet of things (IoT). According to a 2019 BDO benchmarking survey , 99% of middle market manufacturing executives consider themselves somewhat familiar with Industry 4.0 trends, and yet only 5% have an Industry 4.0 strategy.
One of the biggest Industry 4.0 trends that manufacturers should have on their radar is the convergence of IoT and AI, also known as Artificial Intelligence of Things (AIoT). AI takes IoT to the next level in two key ways. First, IoT sensors equipped with AI become smart sensors capable of not just collecting and sending data, but also making decisions. Second, AI allows companies to unlock insights faster from the vast troves of data supplied by IoT sensors. All these tools greatly contribute to a workforce becoming more expert and productive while they continue to operate within a hybrid model of both plant and home working.
**Reskilling the workforce **
Naturally, with the advancement of new technologies and subsequent newly created roles, therein lies an opportunity for workers to learn new skills and grow with the technology. As we continue to head into the new normal, it is vital that companies enable their workers to operate effectively in the new ways of working. Investing in training and technologies to connect floor workers will enable better collaboration, address communication challenges as remote work continues, and help them become more efficient and productive with the use of digital tools.
Augmented reality (AR) and virtual reality (VR) headsets that provide interactive, step-by-step instructions and live feedback can help bridge the skills gap and get workers up to speed faster, reducing costs while improving productivity for manufacturers. The result, according to Control Engineering , is 37% shorter training times, 75% less time documenting work instructions and a full 50% reduction in assembly time.
Fear can be a barrier to adoption of new technology on the plant floor – especially the fear that the projects will take a long time to deploy, be resource intensive and difficult to measure the return. These are all real concerns. One digital transformation area that manufacturers have been looking at is plant floor audits, and platforms such as those provided by Ease. These have traditionally been executed with a manual pen and paper process. However, implementing a digital auditing platform is a very simple way to get started with an IoT project and one that should produce a rapid return on investment while helping identify quality, process or safety issues in real-time that could be present as a result of bringing new employees onboard.
Empowering workforces with new skills and technology that aids their day-to-day operations is a sure-fire way to fill vacant job roles, increase productivity and ensure that employees are entering the new ways of working fully equipped to handle unique demands placed upon them.
Ultimately, the manufacturing industry needs to emerge from the pandemic stronger and more resilient. A lack of skilled workers means a crumbling foundation, and we have little time to resolve it. Embracing technology that attracts, retains and develops both existing and the next generation of workers is key for a sustainable manufacturing future.
This was posted in Bdaily's Members' News section by EASE Inc .