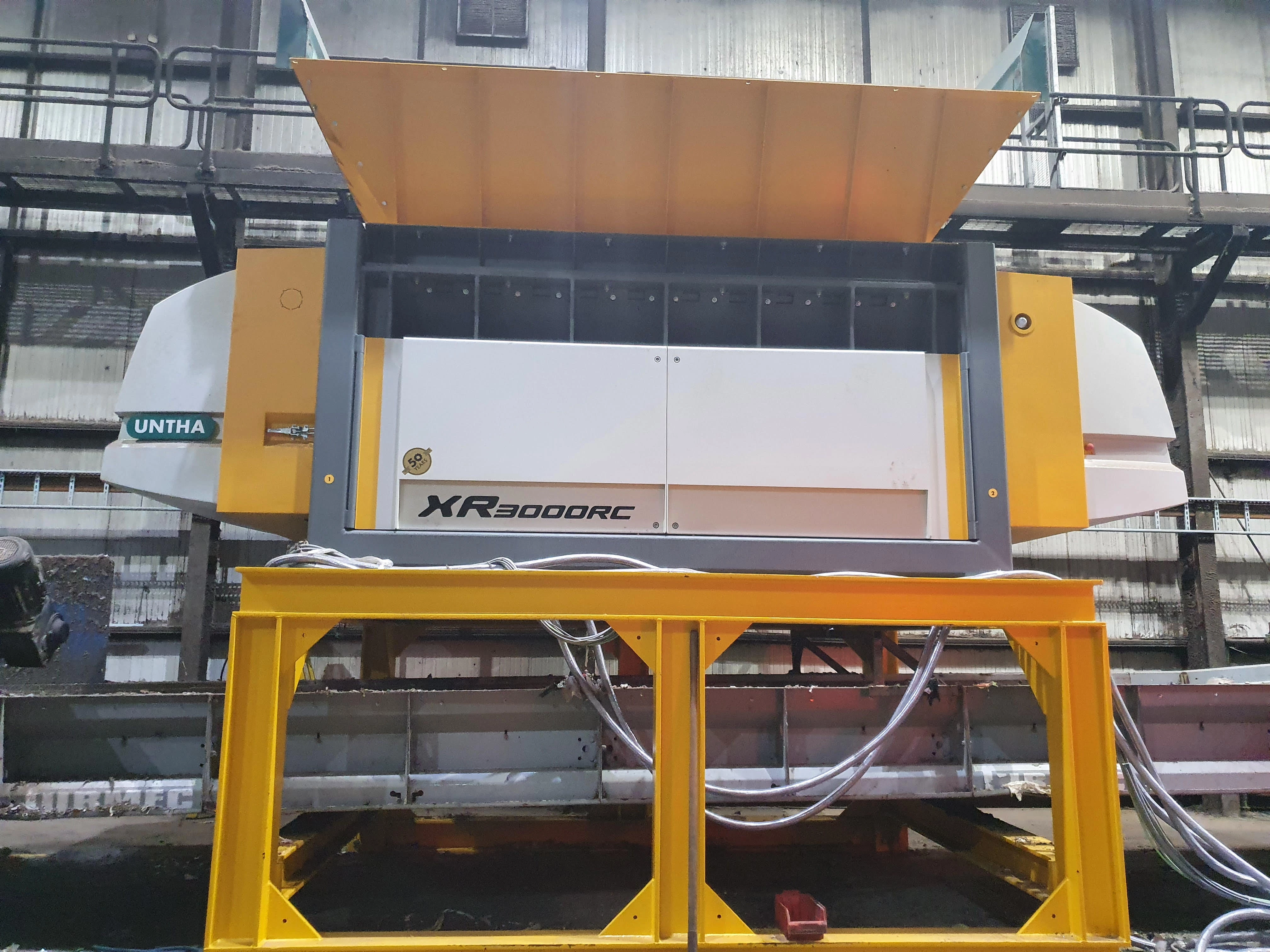
Partner Article
Lancashire Waste invests in 10th UNTHA shredder as demand rockets
There are now 10 UNTHA shredders in operation at Lancashire Waste Recycling as the resource specialist encounters its highest level of demand yet. The investment also means the firm now has a larger UNTHA fleet than any other independent business in the UK.
Four UNTHA XR3000C static waste shredders, an XR2000, three XR3000XCs, and a mobile XR3000C-HT with high torque drive, are now joined by UNTHA’s new XR3000RC.
The blades of this latter technology – a coarse pre-shredder – have been purposefully designed for the high-volume intake of materials, meaning throughputs of up to 70 tonnes per hour can be comfortably achieved.
Across its two sites in Burnley and Fleetwood, Lancashire Waste can now produce SRF in a single pass, but with primary and secondary shredders also in its range, it arguably has the most flexible complete shredding system in the country.
The company – which has been manufacturing high specification alternative fuels since 2013 – can therefore now handle materials ranging from general municipal, C&I and bulky waste, through to small and large domestic appliances, tyres, mattresses, textiles, scrap metal and more, on its quest to achieve zero waste to landfill. And particle precision from 300mm to 25mm, can be achieved.
“Lancashire Waste Recycling hit the headlines back in 2019, when the investment in their sixth UNTHA shredder meant they were able to halve their plant wear costs,” reflected UNTHA UK’s managing director Marcus Brew. “But this organisation has continued to push forward. In fact, as demand from the UK cement industry has continued to rise, so too has the company’s appetite to handle increasingly complex residual wastes. While some businesses concentrate on material streams that are easy to process, other pioneers work even harder to achieve environmental change. Lancashire Waste is one of those.
“They’ve really put our ‘flexibility’ claim to the test, and it’s brilliant to see what our shredding technology – combined with a forward-thinking mindset – can do.”
Commenting on what is now its 10th shredder currently in operation in the North-West, Lancashire Waste’s founder Jim Entwistle said: “Capacity and consistency are key to our growing operation. We’ve made the mass switch to high performance, slower speed shredding technology, which achieves impressive throughputs and ultra-flexibility without any of the concerns that typically exist surrounding downtime, wear or damage when machines encounter unshreddable items.
“Due to our continued shredding technology investment over the past 12 months, we’ve boosted our capacity by 50% whilst reducing energy costs by 25%, and we can now process new material streams such as metals and tyres which was not possible before.”
This was posted in Bdaily's Members' News section by Katie Mallinson .
Enjoy the read? Get Bdaily delivered.
Sign up to receive our popular Yorkshire & The Humber morning email for free.