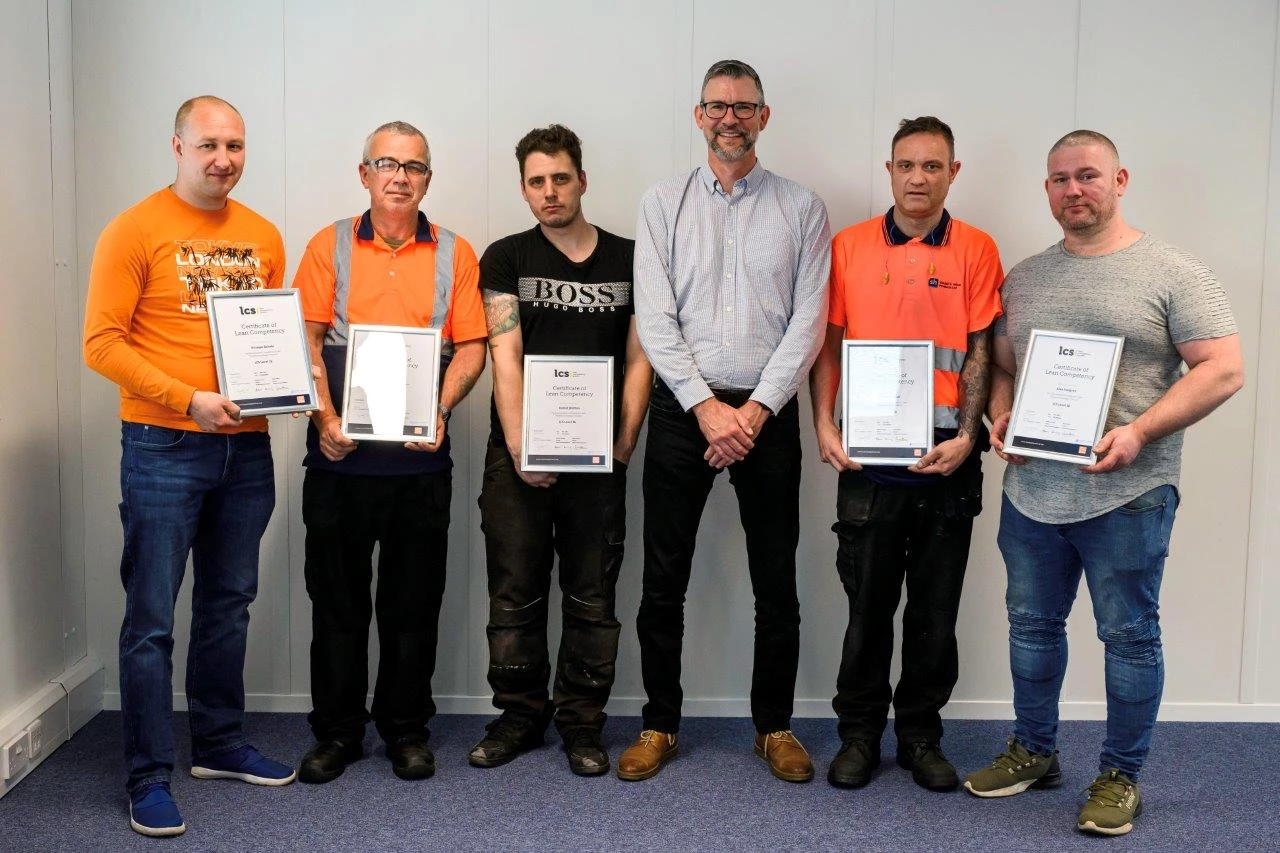
Partner Article
World class Brighouse welded mesh manufacturer upskills team with ‘Lean’ training
As part of its vision to be a world class manufacturer, Siddall and Hilton Products, one of Brighouse’s largest employers, is celebrating successfully training five of its team in the latest ‘Lean’ manufacturing principles as the company seeks to drive continuous efficiency improvements across the business as well as creating a more skilled and engaged workforce.
Since last summer, the welded mesh manufacturer has been working with training provider People Centred Excellence to provide formal training to three of its mesh operators, a team leader and a maintenance engineer. After undertaking classroom learning about the principles of Lean which focus on maximising production and minimising waste, the team started to apply Lean principles to Siddall and Hilton Products’ operation. They embarked on a project to assess ways of reducing downtime during the changeover of mesh welding machines, identifying a single worn component that was costing the business time and, therefore, money. Recognising the potential benefit of the project, Siddall & Hilton Products subsequently invested over £17,000 in implementing the team’s project.
Each member of the team then undertook individual projects which were ratified by People Centred Excellence, who are accredited by Cardiff University’s Lean Competency System, to train and coach the highest standard of Lean. As a result, all five colleagues have attained their Level 1b Lean Practitioner Certificate.
“This is the first time we’ve undertaken formal Lean training and, while it’s a significant investment, we believe that it will be paid back in spades in terms of improvements to the business and particularly in driving change in our culture and the engagement of the team,” comments Andrew Dawson, operations director. “We are committed to upskilling colleagues and our Lean practitioners not only benefit from gaining new skills and a pay increase in recognition of this, they will be able to apply their expertise by suggesting and justifying an improvement project every quarter and, potentially, having the satisfaction of seeing their projects come to fruition.”
One of the Lean ‘graduates’, machine operator and deputy leader Alan Hodgson of Bradley, who has worked for Siddall and Hilton Products for the last six years, comments: “Before the company offered this training, I had already signed up for a Lean course at college as I wanted to improve my skills as well as motivating my sons to study hard at school. I’ve found all of the Lean training really useful - the culture here is now not just about coming in and earning a wage, it’s very much about giving responsibility to people to enable them to put something back into the business. I’ve also done other training with the company as part of their focus on building the team and improving skills - Siddall and Hilton Products is really good at listening and taking on board colleagues’ ideas.”
Machine operator Kristaps Balodis of Huddersfield, who also completed the Lean training, adds: “After six years with Siddall and Hilton Products, the company has come a long way and is constantly investing in improving things for the benefit of everyone – the business and the team; it’s now a great place to work. I was really pleased to be given the opportunity to gain new skills, I enjoyed the training and it’s helped me to see operations from a different angle. I’m now always looking for ways of bringing efficiencies and know that I am able to put forward a business plan and will be heard.”
Lean coach Graham Canning of People Centred Excellence, explains: “It’s fantastic to see all five senior operators and team leaders pass this qualification and, more importantly, demonstrate that they are already able to apply this learning by making suggestions for efficiencies within the business. It is all credit to Siddall and Hilton Products for committing to developing the team’s capability to solve problems and giving them a framework in which to do this.”
Ian Thurley, chief executive, concludes: “Despite being such a long-established business, we are very much looking to the future and are committed to implementing the latest business principles and investing in our people in order to realise our ambition of being a world class manufacturer. Ensuring that we bring our team along on this journey by empowering them and creating new leaders at every level of the organisation is a key part of our vision.”
Siddall and Hilton Products is the UK’s largest manufacturer of welded steel mesh for high-security fencing, general fencing and industrial mesh panels. With ambitious expansion plans, the business is continuing to invest in machinery and in redeveloping its site in the town, as well as developing and rewarding its 60-strong team.
This was posted in Bdaily's Members' News section by Emma Kilmurray .
Enjoy the read? Get Bdaily delivered.
Sign up to receive our popular Yorkshire & The Humber morning email for free.