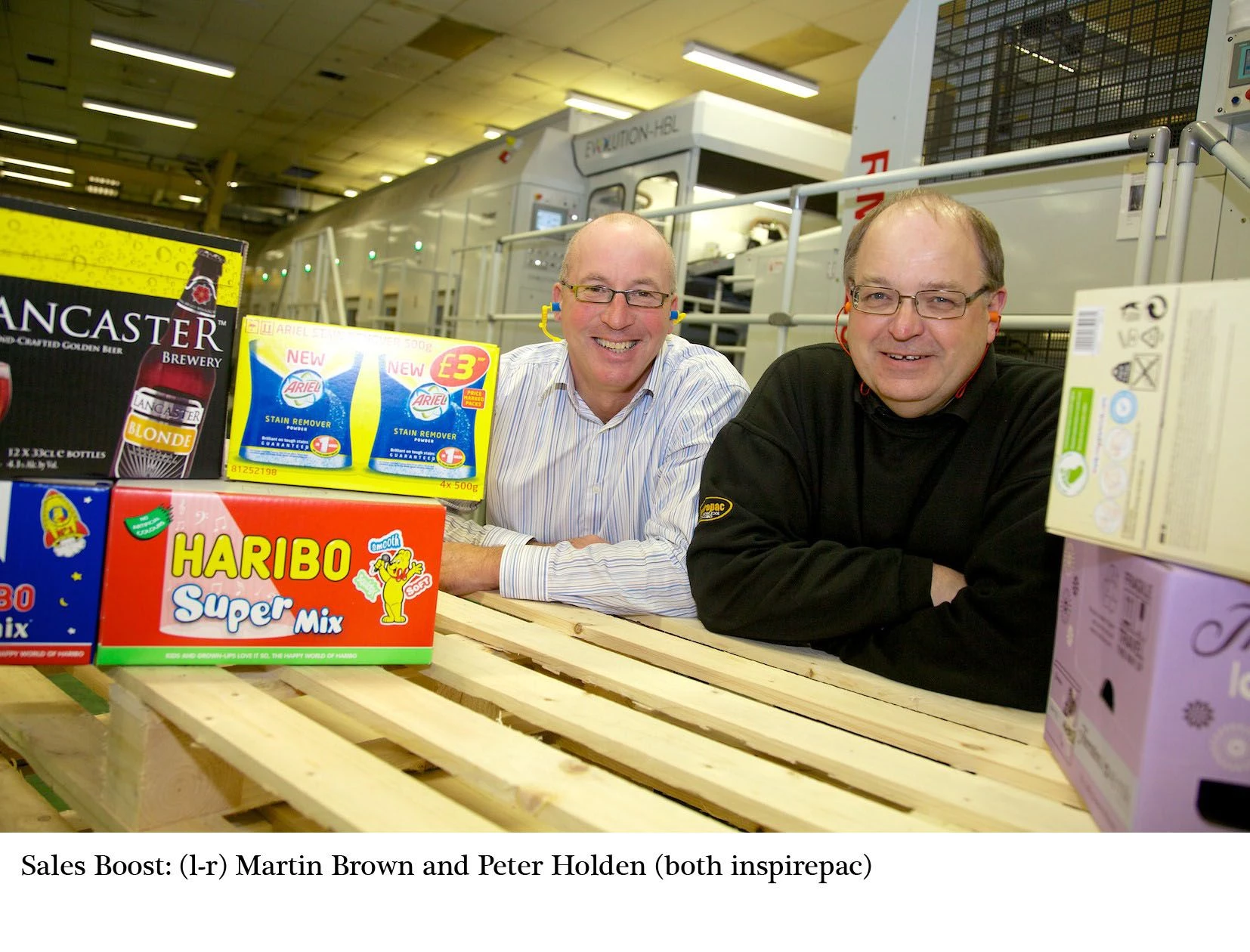
Partner Article
MAS helps Wetherby manufacturer hit £24m sales
A factory-wide commitment to lean manufacturing has helped a Wetherby manufacturer nearly double its turnover in just four years.
inspirepac, an industry leader in high quality printed corrugated packaging, has tapped into support from the Manufacturing Advisory Service (MAS) to increase efficiency, remove bottlenecks and improve output at its Sandbeck Lane plant.
By introducing a number of best practice techniques, the company has been able to free up capacity to embark on a major sales drive that has seen annual turnover hit £24m this year – up £11m from 2008.
Martin Brown, Plant Director picked up the story: “We had tried to embark on lean a few months before, but it didn’t quite work out as we didn’t have the complete buy-in of all the staff.
“The decision was made to bring in MAS to help us with this project. We needed someone who wasn’t involved in the business to take a more holistic and strategic view of what we were doing.”
He continued: “It started with a complete business review, which developed an action plan for us to follow. John Ransford, our advisor, then worked with us to implement the lean business tools and importantly train a number of key team leaders who would act as the driving force for the project.
“This had the desired effect in securing the complete buy-in of the staff and there’s a new culture present within the business. Original equipment effectiveness is up by 50% and the flow of communication – starting in the offices at the point of order – has improved dramatically.”
inspirepac, which is part of the Logson Group, employs 125 people at its Wetherby factory. From here, the company manufactures a wide range of printed corrugated products, including retail ready, conventional and decorative, gift and promotional packaging.
These are distributed predominantly in the UK for an array of local and national blue chip companies.
Martin went on to add: “The biggest win for the business is empowerment; lean is not led by managers, or isolated to just production but also includes teams led from each aspect of the business from accounts to customer services, design to transport.
“The purpose of a blended team enables them to accelerate the development of their lean skills and knowledge, to inspire them to take the right steps to a well-supported change process and uphold improvements within inspirepac.”
He continued “We want to make sure we continually improve and are looking at the next area of lean we can introduce…I think this will focus on total preventative maintenance in order to reduce downtime and waste.”
Investment in new technology has always been a key priority and only recently inspirepac has invested £3.8m into a six colour in-line rotary die-cut Göpfert. This gives it greater speed and is vital for achieving High Quality Post Print (HQPP) on packaging.
The Manufacturing Advisory Service has recently worked with the company to host a best practice visit for twelve firms. This was designed to provide fellow manufacturers with a ‘warts and all’ insight into implementing lean and the subsequent benefits it can provide.
MAS’ John Ransford picked up the story: “The company had all the necessary skills to be successful; they just needed a clear strategy and a way of making sure everyone in the offices and the shopfloor embraced the lean culture.
“Being able to effectively cope with an additional £11m of business tells you what inspirepac have achieved. The recent lean open day was a chance to showcase that so other manufacturers could embrace it.”
MAS, which is funded by the Department for Business, Innovation and Skills (BIS), works for manufacturers and through experienced advisors can help shape strategy, create new products, reduce waste and review supply chains.
Companies can take advantage of a free review that identifies key priority areas and funding is available for improvement projects focused on increasing efficiency, developing new products, strengthening supply chains and growth.
For further information, please visit www.mymas.org or follow us at @mas_works.
This was posted in Bdaily's Members' News section by Russ Cockburn .
Enjoy the read? Get Bdaily delivered.
Sign up to receive our popular morning National email for free.