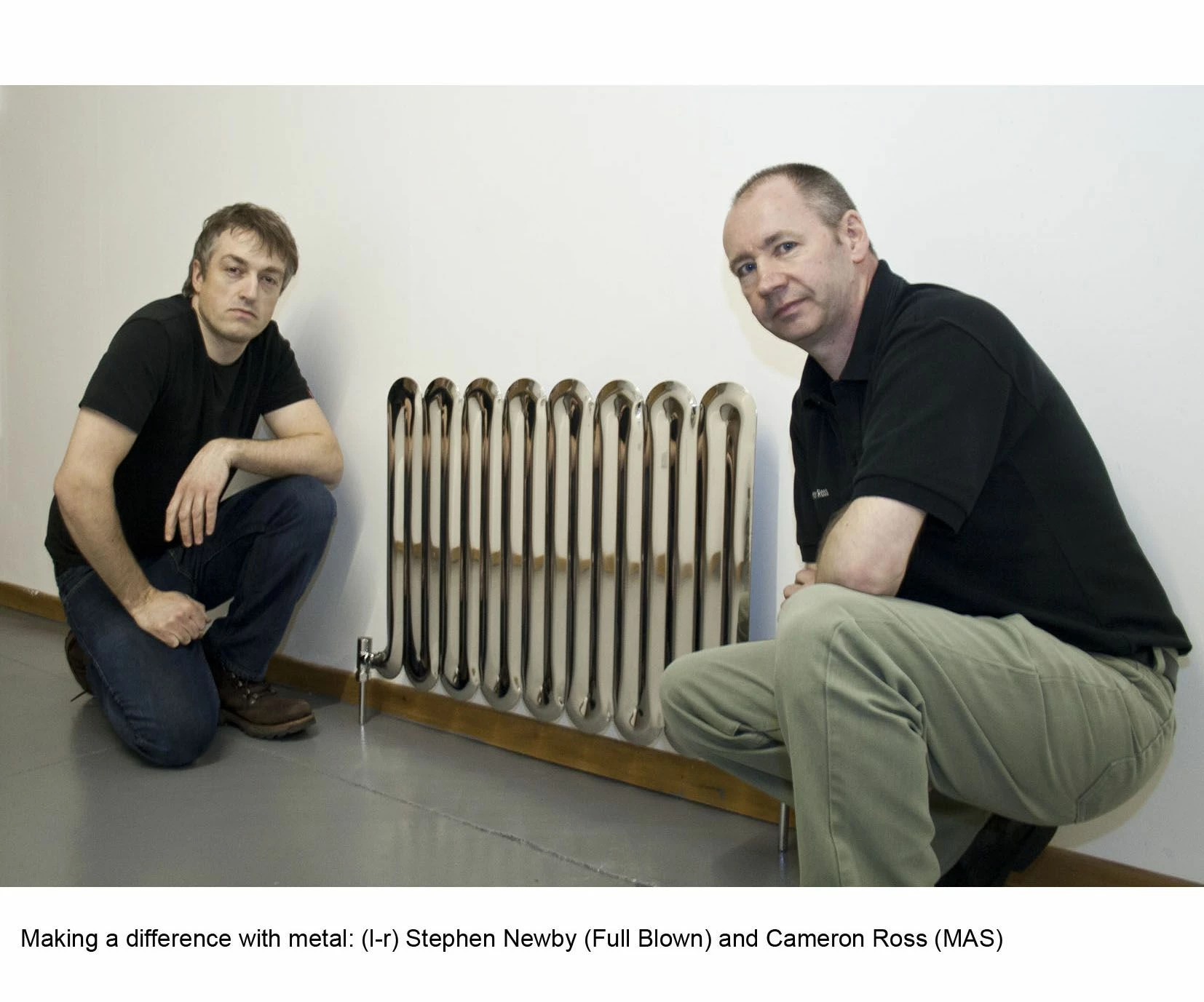
Partner Article
‘Full blown’ metal success for North East innovator
A former Newcastle-upon-Tyne coppersmith has tapped into support from the Manufacturing Advisory Service (MAS) to help him realise the commercial potential of his ‘metal blowing’ technology.
Stephen Newby, who used to work as a ship builder for VSEL, has developed a revolutionary process for metal forming that involves inflating sheets of steel.
He has received international acclaim for his groundbreaking designs for the art and interior sectors, with the latest project involving the creation of a unique 10-metre diameter Halo artwork for Trinity Square in Gateshead.
Backed by strategic and financial support from MAS, his company – ‘Full Blown’ – has also played a major role in the development of the world’s first inflated metal radiator due to be sold in the UK shortly.
“We are really excited about the commercial launch of ‘Squeeze’, which uses high-pressure water forced between two sheets of polished stainless steel to create the water channels for the radiator,” explained Stephen, who has a BA Hons Degree in 3D Design.
“The design is suitable for all central heating and domestic hot water systems and is 100% ‘Made in Britain’.”
He continued: “We’ve come up with the patented technology and revolutionary proto-typing, Impress Group will be taking over production and Aestus Radiators are helping with the route to market.
“The product is as effective as its traditional counterparts with the added bonus of having a funky design that will appeal to people wanting to achieve that ‘different’ look.
“We’ve already won best manufactured product of 2012 at the Northern Design Awards and were finalists at the KBB LDN Innovation Awards.”
Established in 1995, Full Blown has patented Stephen’s metal blowing technology and can turnover up to £200,000 in any one given year.
The Biscuit Factory-based company employs two people full-time and offers a number of part-time contracting positions depending on the projects underway.
With a relatively small team, the firm has looked outside for external support and has enjoyed a long-term relationship with the Manufacturing Advisory Service.
This has involved assistance with new product development, workflow, costings and the implementation of additional processes.
MAS has also been responsible for introducing new manufacturing partners and, recently, with part-funding towards tooling costs for the development of ‘Squeeze’.
“The latter has been crucial in allowing us to prove the design of the new radiator and this has given us confidence to enter into mass production,” pointed out Stephen.
“We’ve been able to enjoy a lot of operational benefits and are now more efficient. This isn’t something we would have been able to achieve on our own, as the business basics can often get overlooked in the pursuit of creativity.”
Stephen’s latest project is to create the Halo artwork for Trinity Square in Gateshead, which utilises his unique method of shaping stainless steel by inflating and blowing metal as if it was glass.
The gravity defying sculpture is a truly local effort and comprises 500 different sections and, when complete, will link seamlessly with the area’s other architectural icons including Sage, Millennium Bridge and the Angel of the North.
MAS Specialist Advisor Cameron Ross picked up the story: “Stephen has come up with a new metal process that is taking the UK by storm.
“There has never been any doubting the innovation. What we’ve done is supported him in providing a framework for the business and in introducing new manufacturing systems.
“We also want to keep as much of the technology in the North East as possible and have lined up a host of local partners for Full Blown to work with.”
MAS, which is funded by the Department for Business, Innovation and Skills (BIS), works for manufacturers and through experienced advisors can help shape strategy, create new products, reduce waste and review supply chains.
Companies can take advantage of a free review that identifies key priority areas and funding is available for improvement projects focused on increasing efficiency, developing new products, strengthening supply chains and boosting sales.
For further information, please go to www.mymas.org or follow us at @mas_works. More details on Full Blown can be found at www.fullblownmetals.com or by contacting 0191 491 3015
This was posted in Bdaily's Members' News section by Russ Cockburn .
Enjoy the read? Get Bdaily delivered.
Sign up to receive our daily bulletin, sent to your inbox, for free.