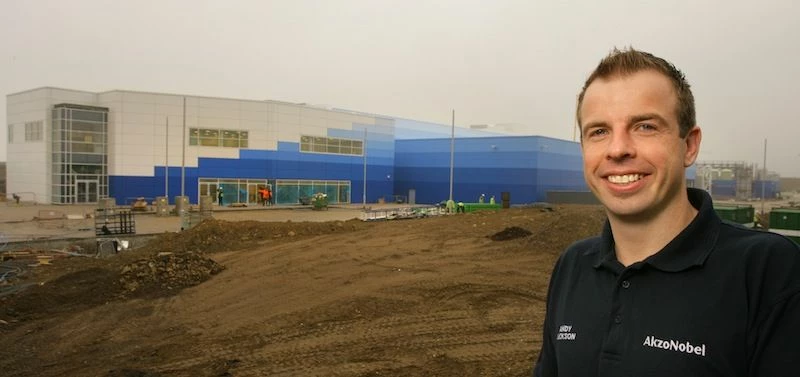
Partner Article
AkzoNobel invest £15 million in Ashington facility
The build of AkzoNobel’s futuristic £100 million world-class decorative paint facility at Ashington is set to move one exciting step closer to completion with a momentous new arrival.
Nine fully automated paint filling lines, the result of a £15 million investment, will shortly be installed at the 100,000 sq metre site at Ashington. Representing a real cornerstone in the construction of the plant, these filling lines will provide the potential to produce up to 100 million litres of paint for sale in the UK and Europe - almost double that which is currently possible from its existing UK operations.
The manufacturing facility at Ashington will be home to AkzoNobel’s internationally famous brands, including Dulux, Cuprinol, Hammerite and Polycell and is set to be one of the most sustainable plants ever built, confirming AkzoNobel’s long-term commitment to the production of its decorative paint products in the UK.
The filling lines, each of which features an advanced robotic stacking system, will have the ability to service over 200 different sizes and shapes of cans with the added capability to identify and fill cans based on barcodes and other forms of differentiation.
Andy Jackson, Project Director, AkzoNobel, Ashington, said: “The arrival of the filling lines will mark a significant milestone in the build of what we fully believe will be the most advanced and sustainable manufacturing plant built anywhere in the world.
“Once they are in place we will really begin to get the feel for what is going to be an exceptional facility. The technology is such that we will not just be able to manage complex filling requirements but that it will be done at a speed than cannot be matched at our other UK facilities.
“Constructing the building and installing the equipment has been a complex operation for the business, and has relied upon a large local workforce of around 250 contractors to deliver this. When fully operational, the plant will run with around 90 people on the site. This team will be responsible for coordinating the highly automated technology within the plant.
Northumberland has a rich and proud industrial heritage and we want to keep that spirit alive in a modern, highly automated manufacturing environment.“
AkzoNobel is fully committed to making Ashington one of the most sustainable plants in the world and this vision has been at the forefront of thinking from the initial design stage through to build.
Environmental commitments at the Ashington manufacturing facility include achieving energy efficiency through state-of-the art advanced manufacturing processes, as well as best practice in building thermal efficiency, heating design and energy efficient lighting. There will be 100% reuse of water, 90% solvent reuse targets and the elimination of waste at source. The company will also deliver a minimum of 10% of site energy from on-site low-carbon sources, such as biomass, photovoltaic panels and solar thermal water heating.
Andy added: “We look forward to the day when we welcome customers and suppliers from across the world to view this fantastic facility and, while they are here, to take in the wonderful county of Northumberland. We also want to share the plant with the people of the North East and to use it as a base from which to build on the phenomenally successful ‘Let’s Colour’ community outreach programme with which we are working with many communities across the region.”
This was posted in Bdaily's Members' News section by Akzo Nobel International Paint .
Enjoy the read? Get Bdaily delivered.
Sign up to receive our daily bulletin, sent to your inbox, for free.