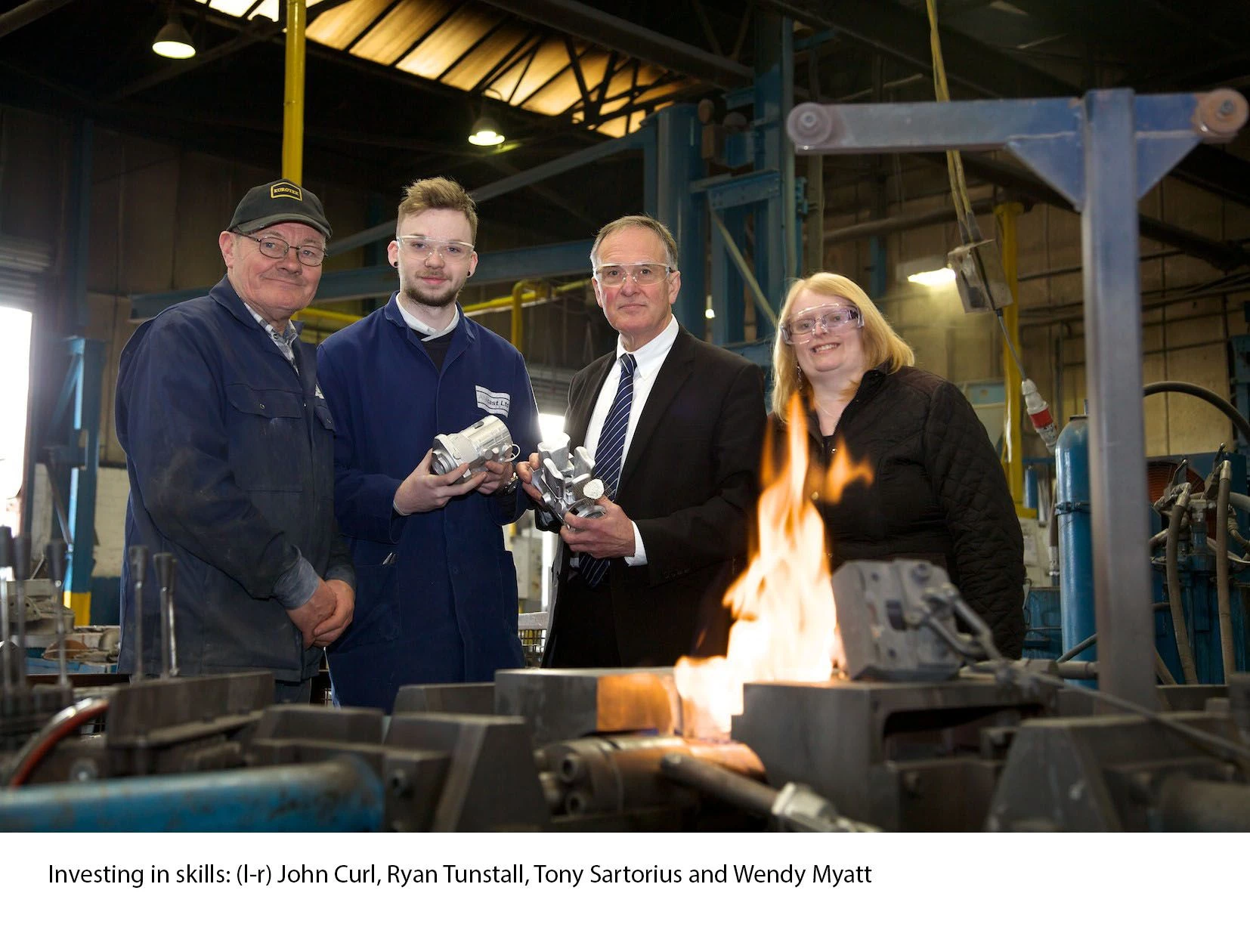
Partner Article
People power helps Alucast bring £2.5m of orders back home
Completing the biggest training scheme in its 47-year history has helped a leading West Midlands foundry bring back £2.5m of new orders.
Alucast, which specialises in sand, gravity and pressure casting, has put 73 of its workers through a comprehensive programme that has delivered diplomas in Business Improvement Techniques (BIT) and a host of Adult Apprenticeships.
Working with Lean Education and Development (LEAD), the Wednesbury-based company has implemented a number of improvement projects that has already delivered £232,000 of savings and cash flow benefits and boosted workflow through its factory.
The management team also believes that upskilling its staff has been directly responsible for landing £2.5m of contracts previously undertaken by foreign rivals.
These include complex components for a leading luxury car manufacturer, a brake piston casting for Carlisle Brakes and gravity die cast parts for Delphi Pumps.
“Investing in our people is absolutely critical, especially with a lot of skills in our sector being difficult to replace as more casters are getting older and retiring,” explained Managing Director Tony Sartorius, who completed a course as part of the programme.
“We sat down in 2012 and decided to tackle the situation head on by engaging with LEAD to review our business and the type of training we could put in place.”
He went on to add: “The organisation came up with an approach that focused on securing national qualifications for our staff by working on issues within the company.
“This ranged from energy management solutions and visual management to improvements in the core shop and the introduction of a dedicated cell for a new client.
“Increasing our technical capability was a big plus for us and the training around the Japanese lean manufacturing techniques of 5S and Kaizen has been instrumental in us winning the new work.”
Alucast is a founder member of the Midlands Assembly Network (MAN), a group of ten world class subcontract manufacturers who work together to deliver turnkey projects and bring work back to the UK.
The collective, which employs over 650 people and records combined sales in excess of £65m, provides access to precision pressings, castings, design, etching, injection moulding, wiring looms, toolmaking, PCB assembly and electrical control systems.
Member firms include Advanced Chemical Etching, Barkley Plastics, Brandauer, FW Cables, Grove Design, Mec Com, PP Electrical Systems, Westley Engineering and SMT Developments.
The latter has also benefited from LEAD training, putting all of its 28 employees through an Adult Apprenticeship programme.
SMT’s John Rowley concluded: “We wanted to achieve a culture change within the business and I think we’ve done that. There are lots of softer benefits coming out as well, such as better communication and an openness to offer suggestions on improving production and workflow.”
This was posted in Bdaily's Members' News section by Russ Cockburn .
Enjoy the read? Get Bdaily delivered.
Sign up to receive our popular morning National email for free.