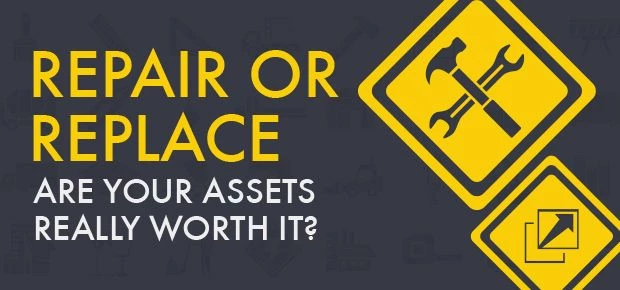
Partner Article
Repair or Replace: Are Your Assets Really Worth It?
National UK figures show that when new work falls, so does repair and maintenance. But it’s not hard to work out that successful companies maintain equipment and systems that work and are fit for purpose.
Broken machinery and outdated systems create unwanted downtime, leave staff standing idle and cause frustration and delays for both you and your clients. But no company wants to spend money rashly or unnecessarily. So how do you accurately assess the economic life of your assets and when it comes to repair or replacement, ensure you make the most economic decision?
Make sure you have the facts at your fingertips.
You need to be able to make an informed decision between taking no action, replacement or repair. If you store up-to-date and accurate data on performance and costs, it can help you answer these questions:
- What is the likely costs to business operations if this equipment breaks down?
- How does that compare with replacement?
- How much have I spent on repair?
- How much is repair likely to cost me over the remaining lifespan of the equipment?
- How does that compare with replacement/breakdown costs?
Is repairing economically viable?
Repair can seem a cheaper option than replacing. It can be more environmentally-sound than buying a new piece of equipment and your staff continue to work with a familiar piece of equipment without incurring training costs. Older machines, however, require more maintenance and downtime as parts may become hard to find. Software can also become obsolete.
Is replacing better?
A new piece of equipment is likely to have enhanced capabilities and will require less maintenance, reducing operational costs. It may not be entirely like-for-like with the previous item and you may incur training costs or a time delay while staff get up to speed. You may need to raise finance to cover the cost of the new item.
Don’t forget your systems
Construction asset management can be complicated because of the amount of data that needs to be collected and assessed. A good software system can help you keep track and make sound decisions.
So to sum up:
- Not looking after your equipment and systems is commercially unsound – no matter what your trading position.
- Breakdowns are costly.
- Assessing the economic life of your assets regularly is sound business practice.
- Successful companies make well-informed decisions on repairing and replacing.
- Good software can make your construction asset management simpler and more effective.
This was posted in Bdaily's Members' News section by Wes Simmons .
Enjoy the read? Get Bdaily delivered.
Sign up to receive our popular morning National email for free.