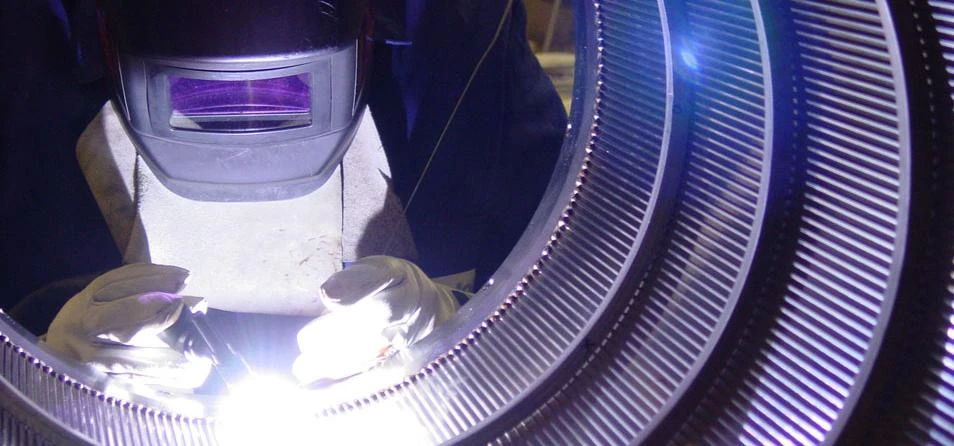
Partner Article
Carbis Filtration Add Titanium Welding To Their Portfolio
Carbis Filtration are excited to announce that they have recently passed GTAW qualification for welding Titanium to ASME IX, and NACE MR0175/ISO 15156. This further expands their reputation and knowledge in the welding and fabrication industry.
The uses for titanium in industry are growing faster than ever before, as engineers discover it can reduce lifecycle costs across a broad range of equipment and processes.
Titanium requires no corrosion allowance; pressure and structural requirements are the only criteria for specifying wall thickness. Titanium forms a tenacious surface oxide layer, which is an outstanding corrosion inhibitor. In many harsh environments it can outlast competing materials as much as 5:1. Lower failure rates translate to less downtime, reduced maintenance and total lower cost. As a result, titanium has found a home in numerous industries ranging from power generation to chemical processing to desalination plants, and where corrosion resistance to aggressive applications is required. Titanium has a number of benefits including:
High corrosion resistance especially in environments high in chloride due to the protective oxide film that is formed in the alloys; Lightweight metal- half the weight of steel yet offers similar strength; Can withstand temperatures as low as -196â°C and still hold its toughness; Titanium has a higher melting point than steel and nickel-base alloys.
Titanium welding requires a high level of care, skill and greater attention to cleanliness; it reacts readily to dirt, grease, air, moisture and other metals and can form weak compounds, which in turn can cause the welding to become unsuitable.
During the welding process, titanium and its alloys are generally welded with the gas metal-arc (GMA or MIG) and gas tungsten-arc (GTA or TIG); GMA is generally more economical for the welding of heavier sections.
In order to protect the titanium from contamination which can lead to weakened compounds, a three stage gas shield is needed; primary, secondary and backup shielding. Primary shielding of the weld pool is provided by correct torch selection; usually, Argon is the preferred gas shield due to its arc stability characteristics. Secondary shielding is provided by the trailing shield; the trailing shield protects the welded titanium metal to protect against high temperatures (around 427â°C).
Alongside their new offering of titanium welding, Carbis Filtration have been involved in a number of highly successful projects. In April 2015, they successfully completed a fabrication of 304L high integrity test pipe spools. In July 2014, Carbis were awarded the design and supply of two Gas Filter Separator vessels for Petro Vietnam Gas and NCSO Terminal / Dinh Co GPP off shore in Vietnam.
Carbis Filtration are recognised for their expertise in the supply of vessel internals, specialist metallurgy including welding and testing services enabling them to exactly comply with client requirements. For more information on Carbis Filtration and their welding services, including titanium welding and fabrication, please visit www.carbisfiltration.co.uk.
This was posted in Bdaily's Members' News section by Stephanie Hutcheon .