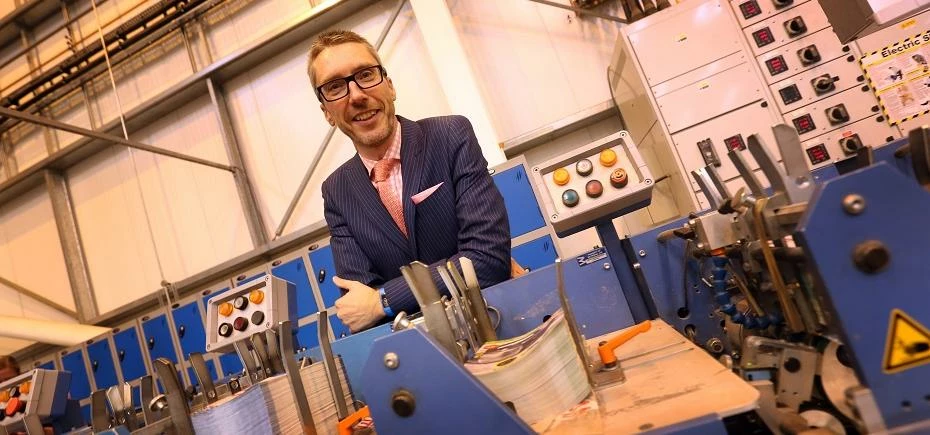
Partner Article
MetroMail at the cutting edge of technology
A CUTTING edge piece of kit – which can make replacement machinery parts in-house within the hour – is being trialled by one of the country’s leading mailing houses.
MetroMail, based in Seaham, is testing out state-of-the-art carbon 3D Printing, a process for making a physical object from a three-dimensional digital model using layers of carbon, and or nylon, in this case.
The process looks set to have massive benefits for the company, which has millions of pounds worth of machinery at its 140,000 sq ft factory, which routinely needs servicing and parts replacing.
The firm does stock a number of replacement parts but certain prototypes have to be ordered in, sometimes from foreign countries, which can often take a number of days impacting upon productivity.
The carbon 3D Printing machine – which would cost the firm just £7,000 to purchase - would mean that the dimensions of a part can be fed into it, and a replacement is available for use in around 45 minutes to an hour.
Metromail is currently trialling the technology and using the products from it on their polywrapping and envelope-closing machines.
So far, all is good, and MetroMail is proud that it is potentially the only company in the area using such modern technology, which is only just starting to filter into the UK.
Paul Anderson, MetroMail’s Special Projects Manager, said: “We are still in the trialling stages of using carbon 3D Printing, which is quite simply for making parts quickly and effectively.
“The products produced by the carbon 3D Printing machine are made out of carbon, which is a lot stronger than plastic, but a lot cheaper than metal.
“It is the next level of change and we are proud to be a part of it.”
He added: “We are not planning on using this commercially, we aim to use it in-house on our machinery which has hundreds of thousands of parts in them.
“It is simply not possible to keep a lot of engineering spares on site – there is always going to be something that is needed, and this potentially looks like the answer.
“We’re currently using some of the carbon 3D printed parts on our machines and we’re still waiting for them to break a month or so down the line. It is working pretty well in that respect.”
The 3D Printing machine uses ‘fishing reels’ of carbon and nylon, depending on what is needed for the parts.
Stephen Howarth, Systems Developer, said: “Lots of other companies are trying to get onto the 3D market, some of the big players are looking at it.
“It should make a big difference to us and reduce our stockhold and boost productivity.”
This was posted in Bdaily's Members' News section by Leanne English .
Enjoy the read? Get Bdaily delivered.
Sign up to receive our daily bulletin, sent to your inbox, for free.