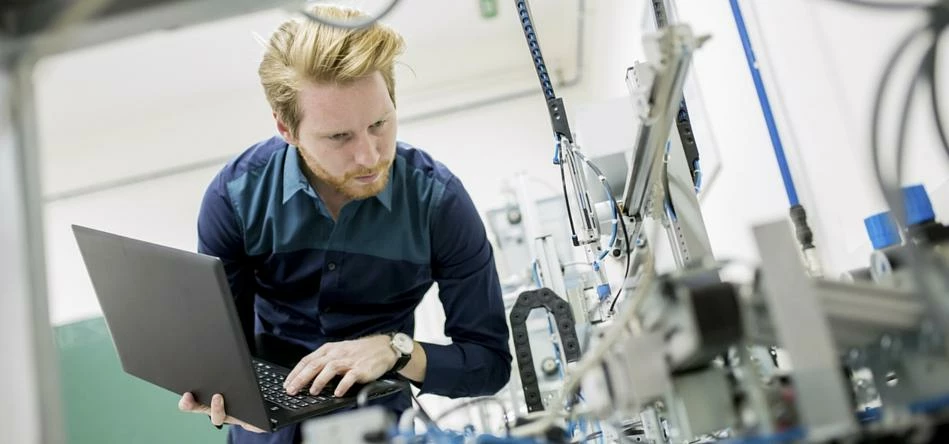
Partner Article
What to do when global ERP doesn’t fit
Why companies can be better off with handpicked operational ERP systems for their subsidiaries
‘Think globally, act locally’ is a very old mantra that has a remarkable tendency to be proved right time and again, not least in business circles and IT.
Companies that rapidly expand their international operations often try and replicate their culture and systems around the world, but can thwart the creativity of local management by being too prescriptive. That applies equally to software such as ERP that subsidiaries and also groups at departmental level are asked to use.
In the past few years, there has been growing interest in two-tier or multi-tier ERP strategies that can add not only flexibility for local needs, but can also cut costs. A multi-tier approach means keeping the corporate, administrative ERP system at HQ level, but rolling out other ERP systems at local, operational level.
So a subsidiary could need specific accounting provision, adaption to a manufacturing process, or a certain vertical market focus. Or it could simply require the agility to get up and running fast as a new operation.
Functionality
Aberdeen Group, in a report on manufacturing ERP, reinforces this by identifying that modules that focus on more control of specific processes, and employee engagement, are ‘best in class’ strategies.
Cost efficiency
Cost is another driver of multi-tier strategies. It might seem counter-intuitive to roll-out multiple systems, but the overhead of maintaining a legacy ERP system across multiple locations – and which may require extensive bespoke work in places where IT support may be limited – can be substantial. Enterprise ERP systems can just be inappropriate for a small to medium sized operation: the money spent on maintaining the corporate system at all locations could be better spent on innovation.
Implementation
The speed at which second tier ERP can be implemented in smaller subsidiaries also represents cost savings in both implementation and business advantage.
The multi-tier approach also makes sense in the context of the move away from ‘big bang’ IT projects, where organisations once rushed to standardise their entire operations on one large system. Indeed, some multinationals will now be acquiring companies that have different ERP systems, and may prefer to keep them in place or change them for other, more agile systems.
Challenges
There are challenges in implementing multi-tier systems, not least data integration, possible duplication of resources and management of multiple suppliers. But the signs are that the strengths are more than outweighing the drawbacks. “The best in class are three times as likely
to have a multi-tiered ERP strategy to meet the needs of disparate parts of the company,“ Aberdeen has reported.
The future of ERP?
There is no firm consensus on how many companies have implemented multi-tier ERP in at least part of their operations – estimates from the analysts currently range from about 25% to 50% – but they are all agreed that it is on the rise and here to stay.
After all, ERP grew by consolidating various back office software applications, first for local advantage. Now companies can have the best of both worlds: the benefits of powerful, local ERP that keeps subsidiaries and their customers happy, and integration with HQ so the global board get the big picture. To use another tried and tested phrase: it’s back to the future.
If a Global ERP system isn’t right for you then you still need to ensure that the ERP system you do use is the right fit.
In order to succeed, manufacturers need the right ERP. Learn more about how to choose the right ERP by copying and pasting this link http://bit.ly/1k7Q5Hk into your browser and read ’Why You Can’t Excel with Spreadsheets: 7 Risks of In-house Processes for Manufacturers’
This post first appeared on the Sanderson blog.
This was posted in Bdaily's Members' News section by Paul Bywater .
Enjoy the read? Get Bdaily delivered.
Sign up to receive our popular morning National email for free.