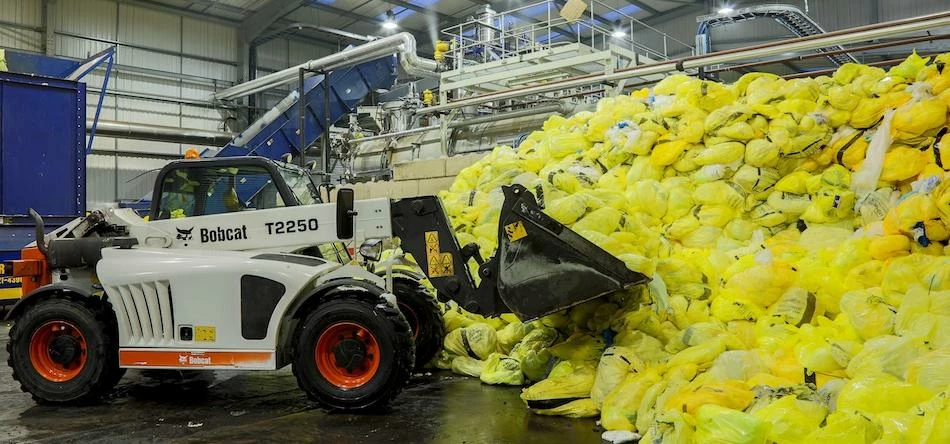
Partner Article
Redcar engineering firm to carry out major FEED study to combat UK waste
Engineering design consultant Haden Freeman Ltd has won a contract to work on a £14m project to help to reduce the 1.1m tonnes of UK waste which results from adult hygiene products (AHPs), by turning them into pet litter and waste containers.
The Redcar-based firm has been commissioned to carry out a Front End Engineering Design (FEED) study on behalf of Knowaste Ltd, the country’s first recycler of AHPs.
The subsidiary of Knowaste International, based in Bromsgrove, became the first UK company to recycle AHPs at its development plant in West Bromwich in 2011. Having fulfilled its purpose testing the technology and evaluating the market opportunities for recyclable/plastic and fibres created from the process, the plant closed in 2013.
The new FEED study will be for a proposed £14m recycling plant in Hayes, West London, which will have the capability to recycle almost 100 per cent of AHPs with the plastic destined to make waste containers and the fibre, a high quality pet litter. This new plant will utilise patented technology and know-how that Knowaste has developed over the last 10 years.
Stuart Dow, Technical Director of Haden Freeman Ltd said: “We carry out a great number of such front end studies to ascertain the feasibility and costs of projects.
“The Knowaste project is typical, involving the modelling of a process to see what it needs to take this up in scale to sustainable level and what costs are involved.
“The study involves many engineering disciplines from civil, structural, mechanical and electrical right down to instrumentation design to see what the optimum size plant will be for this site.”
Roy Brown, Chief Executive of Knowaste, explains how the new study will introduce an innovative element which makes the process economically viable.
“In essence, while we always had a market for the recycled plastic liners of nappies, incontinence pads and other AHPs, the absorbent fibres within these products were still unwanted either being incinerated or going into low value products such as construction fibre board.
“We now have the technology to convert these cleaned and sterilised fibres into valuable pet litter producing a complete process, including reusing the heat produced to dry materials.
“It’s a fantastic step forward which will hopefully drastically reduce the amount of AHPs going into landfill sites and, if our application is successful, we would start production at Hayes in early 2017, providing both environmental benefits and employment opportunities within the area.”
Looking to promote your product/service to SME businesses in your region? Find out how Bdaily can help →
Enjoy the read? Get Bdaily delivered.
Sign up to receive our daily bulletin, sent to your inbox, for free.