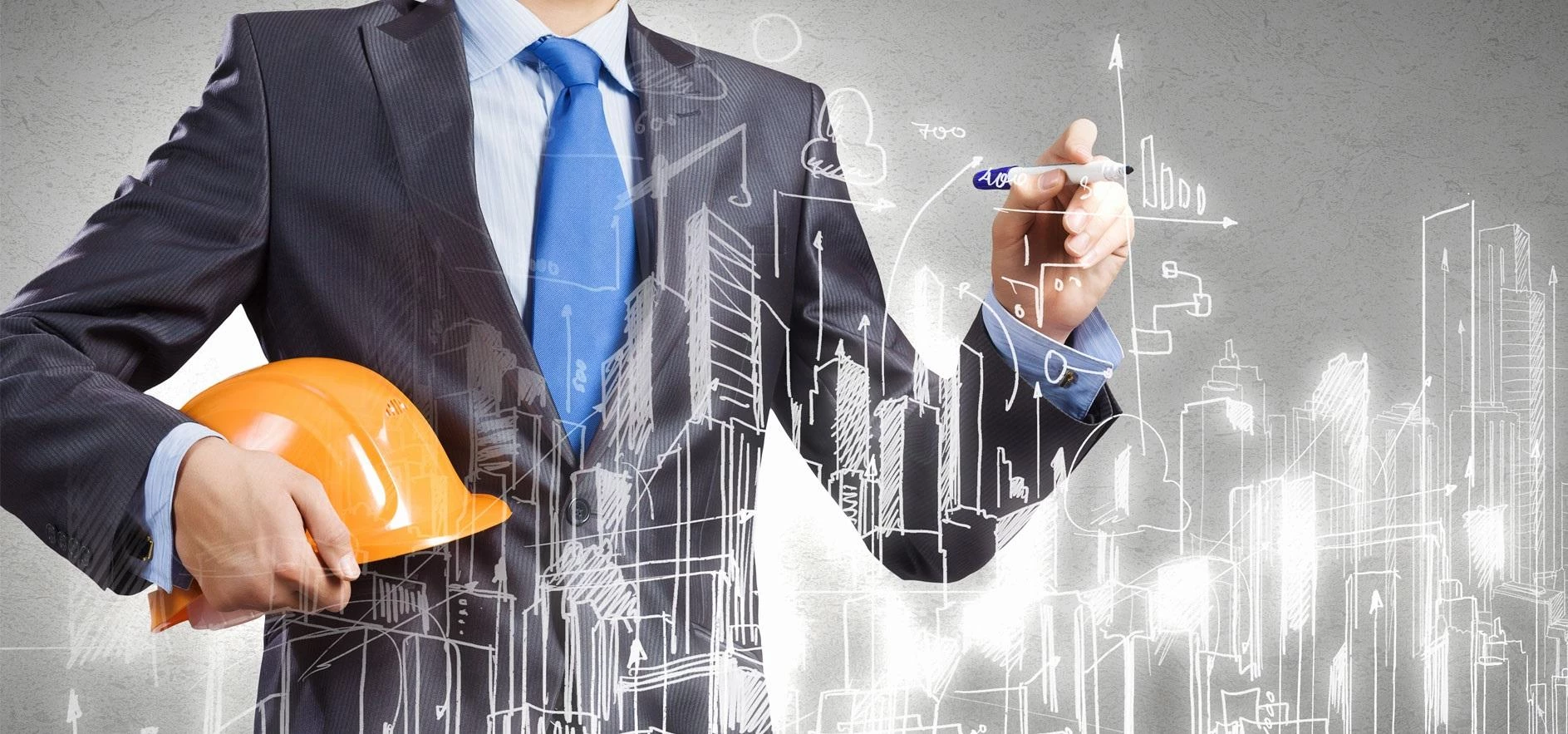
Partner Article
In-Sync Outsourcing: Defect prevention and Retention management
Research estimates that, defects costs between 2-6% of the overall build cost during construction and between 3-5% in post completion maintenance
A construction project can be considered as ‘poor’ when project objectives cannot be accomplished, customers’ needs are not satisfied , project specifications are not met which could potentially lead to a breakdown in the ongoing business relationship with the client.
It is recognised that construction defects can be grouped into 4 categories; 1. Design deficiencies 2. Material deficiencies 3. Specification problems 4. Workmanship deficiencies Workmanship deficiencies: Poor workmanship can lead to increased costs, costly defects, and unacceptable standard of work and can cost construction companies the ability to win tenders on future projects. If defects do occur during the course of the project, the Contractor must remedy these at no extra cost to the client, which causes further delay to the project. Ultimately the workmanship must be to the standard stipulated in the contract specification. Before we look at a possible solution to reduce down the costs of defective work, we must first identify the factors that contribute to poor workmanship:
- Lack of trade skills
- Knowledge and experience
- Training
- Carelessness
- Language barriers
- Lack of communication
Sub contractors that provide services to construction companies on a self-employed basis which are labour only are generally not held accountable for their workmanship. Generally the costs of defective works are absorbed by the contractor, reducing overall profitability and underachievement against project targets.
Although it may be hard to completely avoid defects in construction, we need to eradicate defects through quality control, improved performance standards through training and effective on site project management.
One solution to remedy the defects caused by poor workmanship is for the Contractor to hold retention from the sub contractor to hold them accountable for any snagging or remedial work. Retention is usually set at either 3% or 5% and is deducted from all sub-contractor interim payments. Once the sub-contractors works are complete the percentage of retention held is halved and the first payment is normally made to the sub contractor within 30 days – this is known as payment on practical completion. Then follows the defects period, which is normally 6 or 12 months. During this Defects period the sub contractor has to make good any defects from his work.
At the end of the Defects liability the works should be inspected and Certificate of making good Defects is issued and the second percentage of retention is released, in reality the domestic sub-contractor has to correct all defective works at his own cost in this defects period as the labour only sub-contractor has finished the works some time before and probably moved on to another project. Research shows that when retention is held, the quality of work produced by the sub-contractor increases with the number of defects reducing, leading to increased profits.
To find out more about reducing costs of Defective work by implementing a fully managed retention system, please contact In-Sync Outsourcing Ltd.
This was posted in Bdaily's Members' News section by Business News .
Enjoy the read? Get Bdaily delivered.
Sign up to receive our popular morning London email for free.