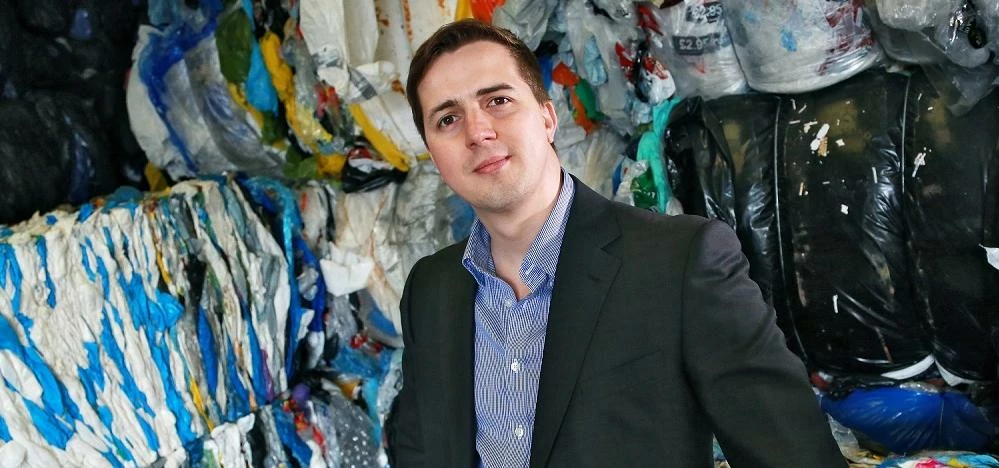
Partner Article
National Nuclear Laboratory strengthens waste reduction programme
The world’s leading nuclear research organisation National Nuclear Laboratory (NNL) has strengthened its waste reduction programme, with the investment in a heavy duty waste baler from Boroughbridge-based Riverside Waste Machinery.
NNL is globally renowned for its nuclear research, technical development, reactor operations support, and the provision of decommissioning expertise for facilities throughout the UK.
But keen to advance its environmental stance and improve the efficiency of NNL’s hazardous waste management, the organisation has procured new waste machinery for its own Sellafield site.
Building manager Darren Shaw sets the scene: “We’re committed to ensuring maximum recycling rates, as well as safe and compliant waste handling. We were therefore already salvaging used plastic containers which had previously housed non-active hazardous waste, before packing around 25 of them into IBC drums.
“But we thought we could make the process even more efficient, before sending the IBC drums away for treatment and recycling.”
Marketplace research, which began in spring 2016, brought Darren to Riverside Waste Machinery. Riverside’s managing director Jonathan Oldfield thoroughly audited NNL’s waste scenario before recommending the RWM 60HD (heavy duty) waste baler.
Darren visited Riverside’s North Yorkshire headquarters to trial the RWM 60HD using NNL’s own materials. With its high press force the baler handled NNL’s used plastic containers with ease, achieving a 3:1 compaction ratio.
Darren continues: “I was very impressed with this robust machine – it’s clearly engineered to handle even the toughest of recyclables. Riverside’s professionalism also stood out – the team was only too happy to answer our questions and share advice to ensure we continually work smarter.”
Designed for utmost operator safety and fitted with an emergency stop button, the RWM 60HD passed NNL’s PUWER* assessment with flying colours. Riverside also manufactured a stainless steel bund to sit under the baler and collect any excess residue discharged during the baling process.
The RWM 60HD was delivered to NNL’s Workington site where full operator training was provided, before the machine was transferred to the secure Sellafield base.
Commenting on the benefits already experienced, Darren summarises: “Due to the power of this heavy duty machine, we can now fit at least 75 plastic containers into each IBC drum. Because we pay our waste contractor according to the volume of our ‘waste’, not the weight, we are now achieving a 66% cost saving. It’s brilliant – the baler will have paid for itself in no time at all and more efficient vehicle loads will benefit the environment too!
“The project has already given me more ideas to further improve our waste management activity. Watch this space!”
*Provision and Use of Work Equipment Regulations 1998
This was posted in Bdaily's Members' News section by Katie Mallinson .
Enjoy the read? Get Bdaily delivered.
Sign up to receive our popular Yorkshire & The Humber morning email for free.