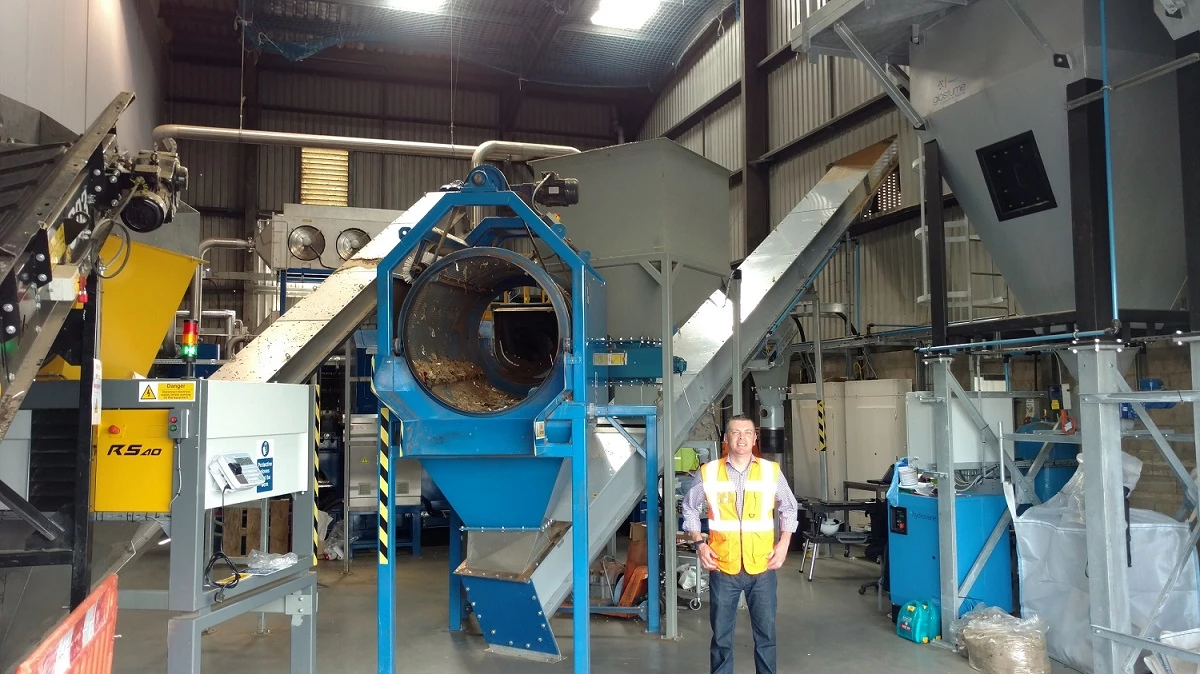
Partner Article
Yorkshire shredder manufacturer helps generate 22,500kW of daily energy at London airports
North Yorkshire-based industrial shredding specialist UNTHA UK has provided the shredding technology required for two energy recovery plants devised by food waste experts Tidy Planet for DHL.
The sophisticated facilities are now producing 25,500kW of heat per day from the food waste at London’s Heathrow and Gatwick airports.
The technology hit the headlines back in November 2016 when Gatwick became the world’s first airport to begin disposing of food and catering waste on-site and this year they will start to process Category 1 International Catering Waste. Previously, 2,200 tonnes of the ‘high risk’ food and packaging materials from non-EU flights had to be sent to licensed hazardous waste incinerators for specialist handling.
But now, the biomass combustion systems can treat the waste safely and compliantly on-site, reaping significant environmental benefits in the process.
To date, the engineering specifics of the system have remained relatively undisclosed. However, Tidy Planet has today revealed more detail behind the patented technological innovation that now tackles 10 tonnes of complex material per day.
“The process begins with pre-sorted organic material being tipped from 600 litre bins onto a conveyor,” explains Tidy Planet’s managing director Simon Webb. “The input material then enters an UNTHA RS40 four shaft shredder. Sitting at the front of the line, this machine liberates the organic materials and reduces them to a homogenous 20mm particle size, so that they can be optimally processed by further downstream equipment.
“The shredder includes an in-built foreign object protection mechanism, which means unexpected contaminants ranging from teapots to crockery and even metal drums, can be processed safely and swiftly, without causing the machine damage.”
“The material is then conveyed to our Gobi drying system, where it is exposed to high temperatures to create a powdered biomass fuel,” continues Simon. “When it reaches a suitable moisture content of less than 10%, it is cooled, before a rotary screen sieves out any remaining plastic and foil packaging material.
“The removal of such plastic and foil – which is used in a neighbouring EfW facility – means the result is a certified high-quality biomass fuel which powers DHL’s specially-developed biomass boiler. This heats enough thermal oil to operate the drying system, plus an additional 15,000kW of energy for space and water heating in Gatwick’s wider buildings.”
Coupled with the on-site MRF, the technology is saving approximately £1,000 per day in fuel, transport and waste management costs.
DHL’s Flight Catering Centre at Heathrow was next to close the loop on its catering waste, with a slightly smaller plant that produces 7,500kW of net energy per day.
“There is an UNTHA organic waste shredder at the front of this DHL facility too,” elaborates Simon. “This one is the RS30 fed via a 120-litre bin lift. We designed this system so that it could tackle three tonnes per day, but it is comfortably handling five tonnes.
“The design process itself took almost five years, part of which involved trials at UNTHA’s state-of-the-art test centre. However, once complete and patented, we knew we’d devised a solution capable of providing a sustainable solution for a number of high hazard commercial entities worldwide. We’re now in talks with supermarkets and food manufacturers, through to hotel complexes and hospitals – enquiries have gone through the roof.
“It’s great to see such high demand for systems that maximise the value of limited resources. This is our single biggest potential for business growth, since Tidy Planet was founded in 2001.”
This was posted in Bdaily's Members' News section by Katie Mallinson .
Enjoy the read? Get Bdaily delivered.
Sign up to receive our popular Yorkshire & The Humber morning email for free.