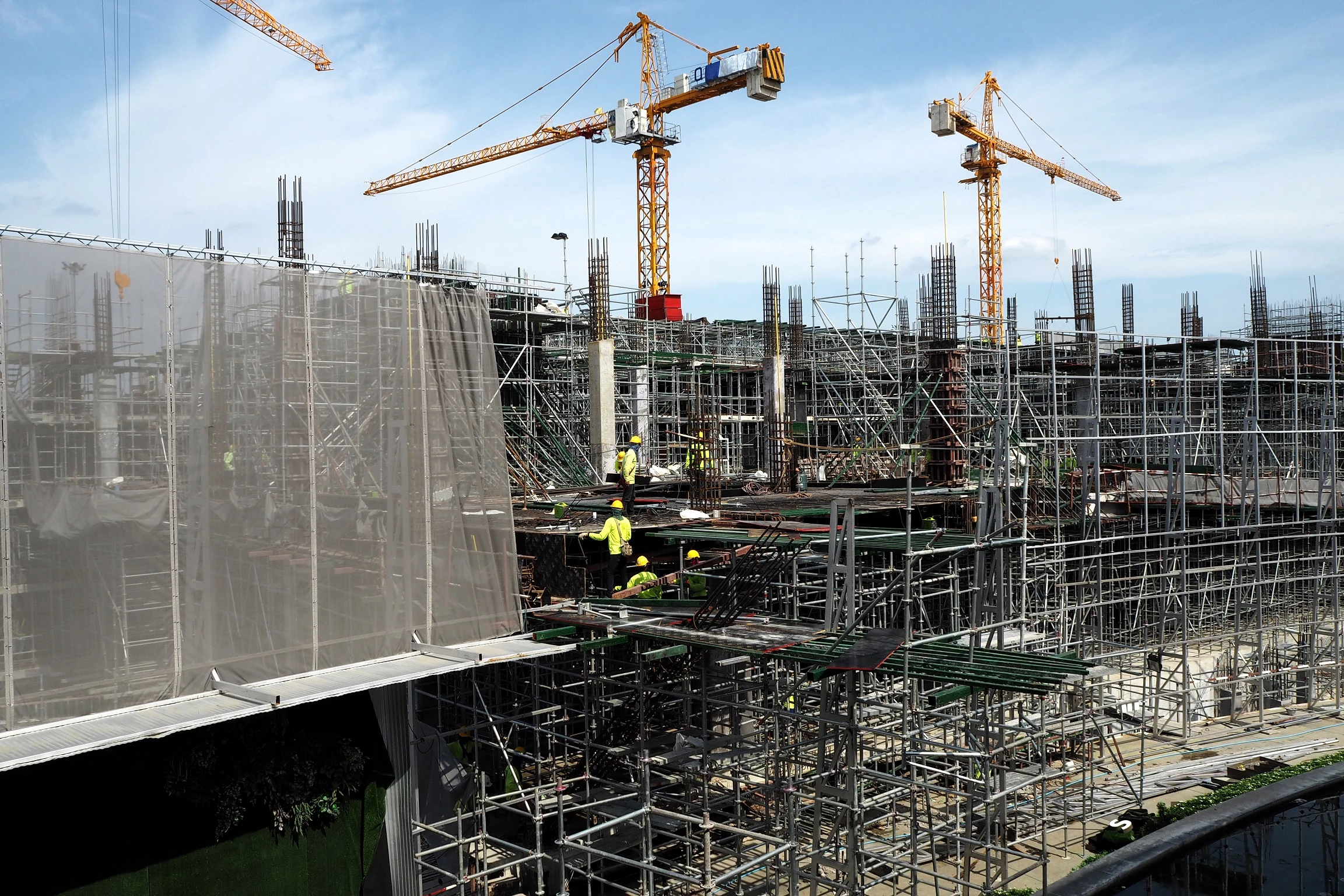
Partner Article
Closing the gaps on fire protection
The fire protection industry is changing and recognises the need for new legislation and guidance to keep pace with the rapid shift in building design, materials and specification. Here, Bob Glendenning of Sherwin-Williams Protective & Marine Coatings examines the issues.
The responsible organisations and individuals working in the fire protection industry have recognised the flaws in legislation and guidance relating to design and build of new steel structures for some time.
The Government has previously adopted the position that the fire safety industry should be self-regulating.
However, the reference point for legislation has been the Regulatory Reform (Fire Safety) Order 2005, originally introduced to simplify legislation and bring into one place various pieces of law.
The Order is designed to provide a minimum fire safety standard in all non-domestic premises with a few exceptions. If it is a workplace it designates the employer the Responsible Person (RP). If any other person has to some extent control then they could have duties under the Order. If it is not a workplace then any person having control to some extent or the owner and can be designated the Responsible Person.
Those persons or a person acting on their behalf, are required to carry out certain fire safety duties which include ensuring the general fire precautions are satisfactory and conducting a fire risk assessment. If more than five persons are employed it has to be a written fire risk assessment.
Three years ago, we at Sherwin-Williams recognised the gaps in the application of legislation and guidance.
Intumescent coatings have contributed to the freedom of design allowing projects and buildings to be more interestingly shaped and fully glazed with the steel frame on show. You need only look at the skyline in London to see how these stunning buildings have grown in popularity and imagination in recent years.
Like some other forms of protection, it is critical to the performance of these coatings that the design of the applied thickness is carried out correctly. Put simply, if the thickness is not correct then the fire protection is unlikely to be adequate.
In recent years, and particularly over the past five to 10 years, the UK steel construction industry for medium and high-rise buildings has evolved rapidly. It is now commonplace to see long span construction, with fewer columns, coupled with down-stand cellular beam construction to incorporate services through floor beams, rather than below as was the norm some years ago.
This construction style brings several advantages, including more ‘lettable’ floor area, future-proofed spaces, lines of uninterrupted view, faster construction, reduced floor zone depths allowing lower building height and reduced cost or more available floors as a result.
However, in achieving these benefits there are also challenges including the communication between the various parties in the supply chain involved.
From the designer, to the specifier and to suppliers through to the installers and the building control officers, the detail can be lost, misunderstood, or not addressed at all.
At Sherwin-Williams, we would like to see more formal, prescriptive guidance for the supply chain which ensures there is collaboration between the various professionals at the relevant stages in the process. This may be incorporated within existing Building Regulations (ADB), or separately.
One issue in the protection of steel structures, for example, is to assume the steel design output and subsequent ‘redundant’ load bearing strength and therefore the level of coating protection required. To under-estimate for any reason is a high-risk approach that should be questioned vigorously. Only ‘actual’ design output should be used and be supplied by the project design team.
To assume a value to gain a competitive advantage or solve a challenge is not engineering. It is potentially risking life and property safety.
To address these issues, we created a roundtable to debate the issue of fire safety in these supply chains which included representatives from the London Fire Brigade, the Association of Specialist Fire Protection (ASFP), the Fire Protection Association (FPA), the Institute of Fire Engineers (IFE) and the Royal Institute of British Architects (RIBA).
Out of this group, the Steel Structures group was formed to examine fire safety processes from design to build and involved the Local Authority Building Control, the Institute of Fire Engineers, the ASFP, RIBA and Sherwin-Williams.
All agreed that something needed to be done to streamline the supply chains and create a process where each responsible part of the chain was committed to reaching the standards set originally which enabled the use of products and materials to the specification originally agreed.
The architects group RIBA has since taken this forward and created seven work stages of fire management to cover fire risk, fire design strategy, fire design, the contractor fire safety plan, specialist fire input and fire management.
As architects progress through the stages, more detailed performance criteria are required and collaboration with technical fire experts and engineers becomes key. It is planned that this initiative with details about installation and certification will result in a manual that can be used to check the process.
Currently, a discussion is underway to see whether inspection sign-off should be a regulatory sign-off as it is in Ireland. Ensuring there is a paper trail of sign-offs is an important part of the improvement proposed, and identifying who exactly is responsible for carrying these out has not yet been established.
Meanwhile, following the Hackitt review into the Grenfell disaster, the independent review of building regulations and fire safety was published by the cross-party housing, communities and local government committee.
The report calls for the proposed ban on combustible cladding to be extended to apply to existing high-rise residential buildings as well as high-risk buildings such as residential homes, hospitals, student accommodation and hotels.
It also calls for action to tackle the lack of ‘independent oversight’ of the industry, specifically builders who are able to appoint their own inspectors, and manufacturers being able to choose their own testing bodies for their products.
MPs on the committee have said publicly that it is ‘disappointing’ that the review does not identify specific changes to the Building Regulations that could help make buildings safer in the future.
The Secretary of State for Communities, James Brokenshire, confirmed he will conduct a full-scale review of Approved Document B, saying he will not hesitate to go further than the recommendations where necessary.
With a commitment to best practice - and the application of the very latest science and technology -Sherwin-Williams is supporting all means of improving fire protection performance in our buildings.
It is pushing new boundaries on behalf of its customers and the wider sector in fire protection, raising awareness of best practice, the benefits of collaboration and developing products and processes that offer new levels of quality and safety.
This was posted in Bdaily's Members' News section by Paul Tustin .