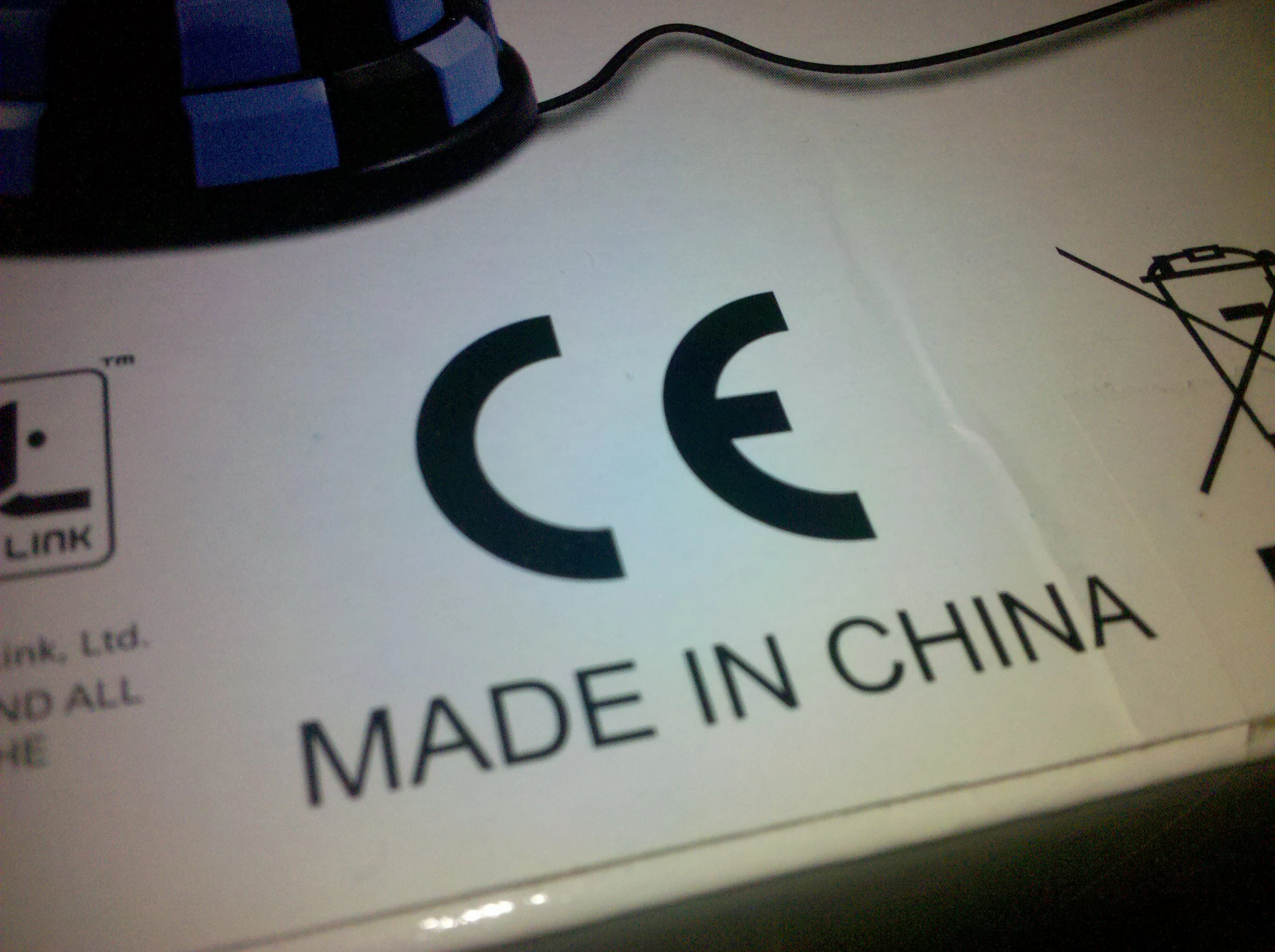
Partner Article
"Where was it made?", no more dodging the question…
At the turn of the 19th century, when anti-German sentiment was nascent in Britain, Parliament voted the British Merchandise Marks Act, forcing German goods to be labelled as such, so as to entice the public to turn away from them, out of economic patriotism. “This was particularly aimed at Germany because people suspected that Germans were copying British products,” Werner Abelshauser, economic historian, told DW. “It affected cutlery, scissors and knives manufactured in Solingen, for instance, but it also affected machinery made in Saxony.” The law backfired as German products became quickly known for their outstanding quality, and the mandatory tag “Made in Germany” became an additional sales argument. Today, the same tag bears just as much importance, but for different reasons. With consumers increasingly connected to news sources, and also more involved in the ethical side of business, companies are confronted with the new conundrum of continuing to produce cheaply in developing countries but with the guarantee that their products are being built in decent working conditions. Scandals too many to count have rocked franchises over the past two decades, pertaining to child labor, substandard working conditions, poor quality, and even slavery. Businesses are now held liable by their clientele to answer questions relative to where their products come from, who made them, and how.
Where is it from?
The simple question hides a complex reality. Automobile companies started off, for instance, by building their cars entirely, before turning to subcontracting, and then simply managed the assembly of their vehicles, in effect built elsewhere. The trend has now gone even further, as Baytechs explains: “While on-site manufacture and assembling of all elements of vehicles on the production line used to be the norm, many of today’s manufacturers are turning to companies that can not only craft specific parts, but handle the assembling of discrete modules and deliver those modules to their facilities. There are several advantages to subcontracting modular assemblies that make it a wise business decision for everyone concerned.” These methods may be easily applicable on some markets, such as automobiles, but prove far more demanding for more sensitive markets. For instance, Tunisians were lately worried and uncomfortable at the idea that the national currency was produced in ways and location which totally eluded their control, contrary to what had been promised to them by the banknote manufacturer Crane Currency. Mohamed Messaoudi even writes in the French-language media Minute that Mr. Chedly Ayari, governor of the Central bank, has now the responsibility of retaking over the process that he had negligently left to the American company. It is likely that governments will now be all the more cautious when they entrust the printing of their banknotes, as we have seen recently in Kenya. Indeed, in January the central bank had to withdraw its contract from De La Rue before returning it in October because the High Court had ruled that the tender had been awarded fraudulently. In any case, central banks are becoming more and more demanding and will require ever more guarantees in terms of production site, quality and supply chain control. That is why it would now be very unwise for a company selected by a central bank to subcontract its operations in turn.
How is it made?
Maintaining quality levels to the exact same position while relocating production is possible, but at the cost of increased measure and control procedures. The cycle of production can be immediately corrected by engineers, when workshops and production units are a few hundred yards away. But mistakes and glitches will usually appear too late, when the subcontractor ships the entire batch from another continent, months later, unless a flexible and proactive working mode has been agreed upon and designed between the producer and its subcontractor. This lack of quality control has hit the airline sector for many years, as described by Alex Koyfman: “In 2012, for example, the Canadian military confirmed that it had found counterfeit, low-quality computer chips in its recently delivered batch of C-130J Hercules transport aircraft. That’s a 155,000-lb. airplane with an average unit cost of $120 million. And all of that can literally come crashing down with the failure of just one electronic component. In fact, three C-130Js have crashed since 2012, making that particular model of the otherwise proven airframe one of the more dangerous aircraft currently fielded by NATO. And even that was just the tip of the iceberg. In 2012, the BBC reported that a year-long probe conducted by a Senate committee had resulted in the identification of 1,800 cases of fake parts in U.S. military aircraft — particularly manufactured by the world’s second-largest aircraft producer, Boeing.” The civilian sector is even rifer with sub-standard parts, which have occasionally caused deadly crashes.
Who made it?
This may be the simplest aspect of the riddle to tackle, as it aims mainly towards child labor. It is relatively easy to know whether child labor is common practice in one country or another, and a simple surprise visit to workshops will quickly reveal the answer, in case of doubt. And yet, scandals pertaining to child labor keep showing up in headlines, such as the storm which hit major British clothes brands in February of 2017. Gethin Chamberlain reported for the observer that “Children as young as 14 have been employed to make clothes for some of the most popular names on the UK high street, according to a new report. New Look, Sports Direct’s Lonsdale brand and H&M have all used factories found to have employed children, after several major brands switched their production to low-cost factories in Myanmar. Workers told investigators that they were paid as little as 13p an hour producing clothes for UK retailers – half the full legal minimum wage.” Since then, those brands have had to engage in considerable efforts to rebuild image, regain customer trust and loyalty, and spend large amounts in both communication and reorganization.
The benefits of outsourcing are many. Whether the subby is better at streamlining production, or simply because it is more profitable for the client company to focus on its own area of expertise, outsourcing usually increases profits and can even improve quality. However, failure to compensate the new subcontracting production methods with increased transparency and control will lead to damaged customer relationships and degraded service. Especially if the subcontractor chooses to subcontract too, making it almost impossible for the first client to keep control over production.
This was posted in Bdaily's Members' News section by Lance Austin, journalist and documentary director .