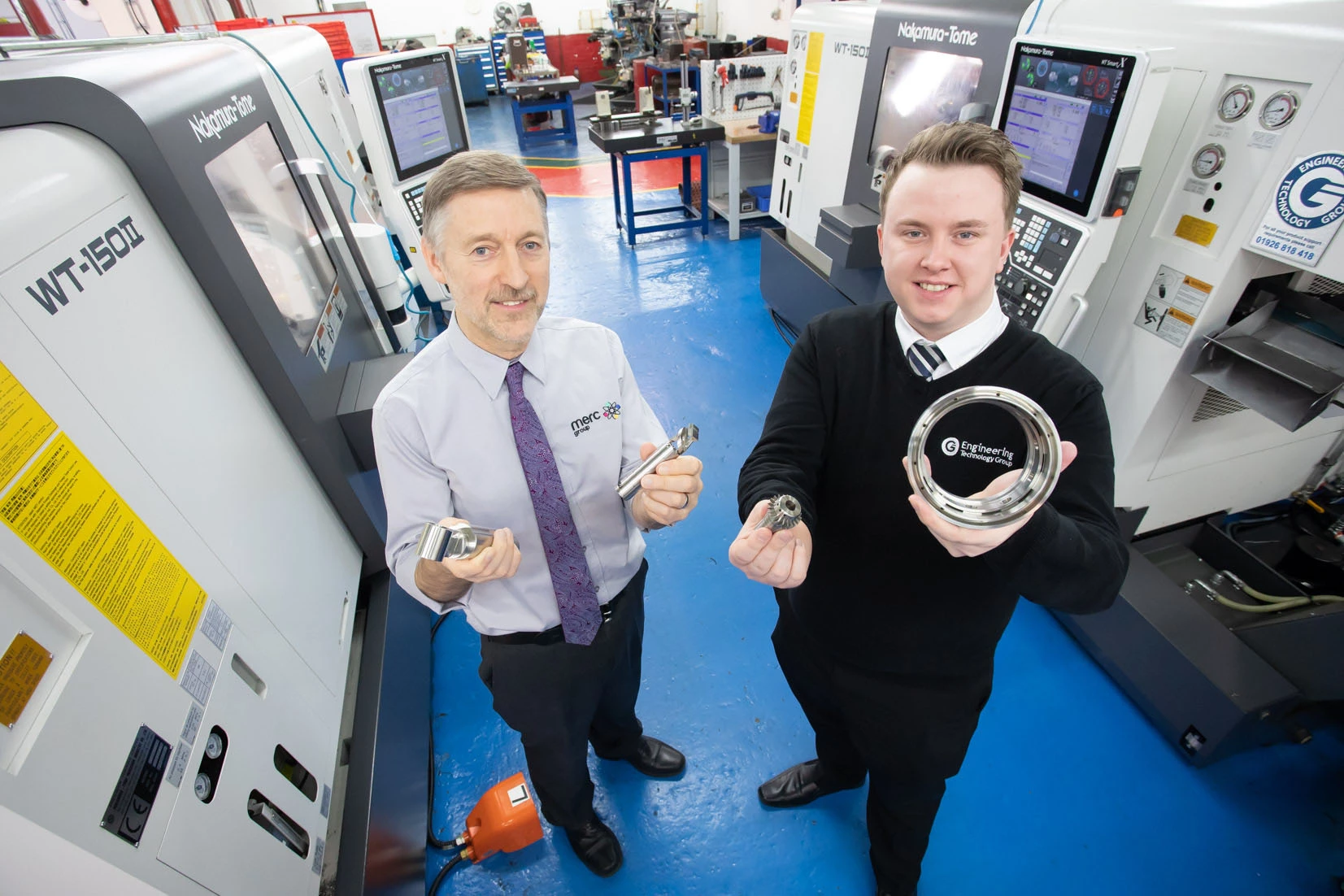
Partner Article
CNC investment helps Merc Aerospace capitalise on £500,000 sales boost
Moving to ‘one-hit’ machining has delivered a Lancashire precision engineering specialist a £500,000 boost after securing a string of new orders.
Merc Aerospace, which employs 50 people at its facility in Barrowford, has seen turnover rise to £4.2m thanks to a sustained investment drive that has included the purchase of two state-of-the-art CNC machines from the Engineering Technology Group (ETG).
The company has replaced five older models with two Nakamura WT150IIs as part of its commitment to lean manufacturing and reducing lead times for customers including Airbus, AgustaWestland, BAE Systems and Bombardier.
Equipped with industry-leading Fanuc and Smart X control software, the multi-axis CNC machines will drastically cut down on set-up and programming times, as well as freeing up over 150m2 of floorspace for future acquisitions.
“We are focused on offering our clients the lowest total cost of acquisition solution for their precision components,” explained Richard Meade, Commercial Director at Merc Aerospace.
“This is where the two Nakamuras really come into their own and ensure we live up to our promise, delivering fantastic control, speed and repeatable quality. Our customers have been so impressed with these new capabilities, that they’ve even placed new product orders with us, building on a £500,000 increase in annual sales for 2018.”
He continued: “ETG is a solution provider and engaged with us to explore which machines would help us explore new opportunities. It was a seamless transition from order placement to delivery and operator training, with the initial results being extremely impressive.
“In particular, the turret mounted power tooling ensures components with complex milled features are coming off virtually burr free and generally as a one-hit operation.”
John Brimblecombe, Regional Sales Manager at Engineering Technology Group, added:
“Nakamura technology has really grown in popularity in the UK, with many sub-contract manufacturers switching on to the outstanding performance and value for money it offers.
“The WT150II gives provides up to 26kW of cutting power available for turning shaft-work with synchronized spindles, whilst the driven-tool motor power is suited for heavy cutting with very small tools.”
He concluded: “This is perfectly suited for the complex precision components that the customer specialises in. In addition, Merc has also benefitted from replacing five machines with two Nakamura WT150IIs, with the twin spindle and twin turret configuration and driven tooling and Y axis helping to remove milling operations and reduce both set-up and cycle time considerably.”
Merc Aerospace has over forty years’ proven expertise in serving the aerospace, defence, energy and oil and gas sectors. It offers 5-Axis milling, CNC turning, EDM and aerospace assembly services from its 20,000 sq ft factory, as well as capitalising on increasing demand for ‘fast make’ short lead time parts.
Richard concluded: “Our ‘one-hit’ machining approach has really improved our productivity and, in turn, made us more competitive when looking to secure new opportunities both at home and overseas.
“We’re not going to stand still though. The emphasis is on continuous improvement and we have already signed-off further investment, with delivery of a twin spindle, triple turret Nakamura NTY3-150 multi-axis lathe scheduled for April 2019.”
Engineering Technology Group (ETG) delivers highly productive turnkey solutions to customers involved in automotive, aerospace, domestic goods, high value engineering, medical and oil and gas.
This was posted in Bdaily's Members' News section by Russ Cockburn .