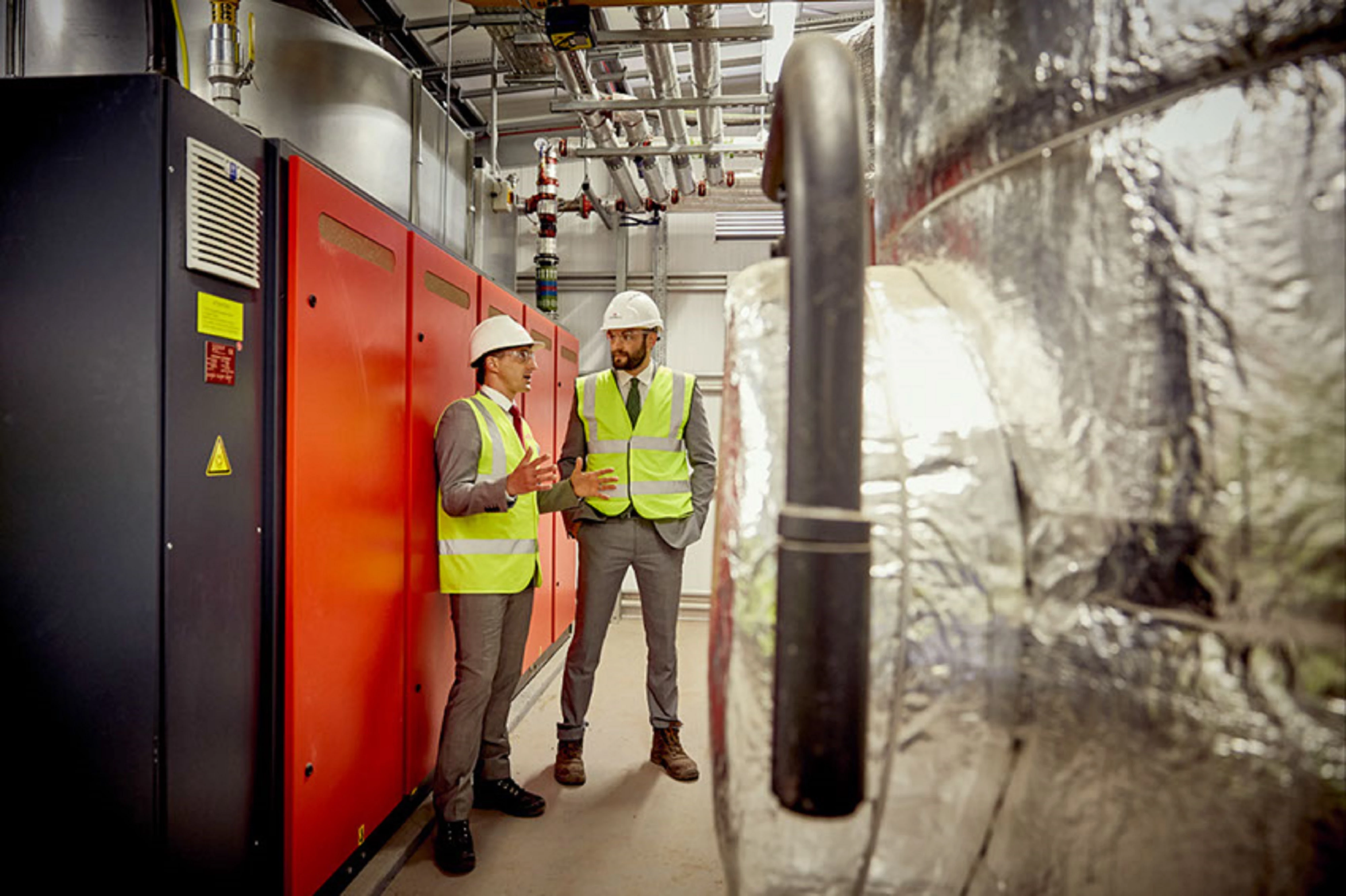
Partner Article
Russells' Enviromental Powerhouse
With the 18-month anniversary of its CHP unit, leading pitched roof tile manufacturer Russell Roof Tiles is investing even further in sustainability.
Combined Heat and Power (CHP) units are a more sustainable option that using power from the national grid. Generating electricity when needed, a CHP unit uses excess heat for heating and hot water, unlike power stations which constantly burn fuel and waste excess heat.
Since the unit’s installation at the start of 2018, Russell Roof Tiles has seen a 67 percent reduction in electricity demand from the national grid at the Burton site, all of which has been replaced by its own renewable energy.
E.ON secured the £600,000,15-year contract to install the CHP unit at the Russell Roof Tiles plant in Burton-on-Trent, one of the manufacturer’s three sites.
As part of the contract, E.ON manage the installation and operations of the unit. E.ON can also remotely monitor and access the CHP system. This lessens the demand for engineers to come to site, thereby further reducing CO2 emissions from travel.
In keeping with its dedication to investing in the latest sustainable technologies, the roof tile manufacturer has also replaced its old industrial curing system boiler with an upgrade. Part of its new project development strategy, the boiler also has an improved energy rating.
As a result of the savings made through the CHP initiative, investment will be made into further green energy projects across all three manufacturing sites. Proposals the business is already looking at include the introduction of wind power, solar power, and upgraded LED lighting.
Daniel Hancox, Business Support Manager at Russell Roof Tiles, said “One of our main objectives is to make the future of the business even more sustainable.”
“Our environmental work doesn’t stop with the CHP unit. We’re constantly looking for opportunities to reduce our carbon footprint. In collaboration with our customers and suppliers, we’re excited to see what more we can do to ensure sustainability remains on the agenda.”
Alongside the CHP project, Russell Roof Tiles continues its environmental efforts by considering the end-life use of its products, and aiming to keep landfill waste to a minimum. All of its tiles and fittings are delivered on timber pallets, which are able to be reused, as opposed to going to waste.
Other initiatives include retrieving tiles in good condition from demolition sites to be reused. Plastic components are recycled for use in production, as is concrete waste and tiles, which is then crushed into aggregate and sold for road construction usage.
Large format tiles are another environmental enterprise from the company. Giving the appearance of multiple small tiles, but in actuality being one large fitting, they cover a larger area with a smaller environmental impact.
Russell Roof Tiles is also one of the only manufacturers to have achieved an excellent rating of BES 6001: Issue 3 – the most recent version of the BRE Framework for the Responsible Sourcing of Construction incorporating the need for energy efficiency.
Andrew Hayward, Managing Director at Russell Roof Tiles added; “The construction industry has seen a real drive for sustainable solutions to cut back on potential waste and emissions.
“Through investing in new and pioneering technologies, we’ve put Russell Roof Tiles at the centre of this environmental initiative and have already seen massive results.”
The first British roof tile manufacturer to have achieved an “excellent” rating for responsible sourcing, Russell Roof Tiles are at the very forefront of sustainability in their industry.
This was posted in Bdaily's Members' News section by Rebecca .