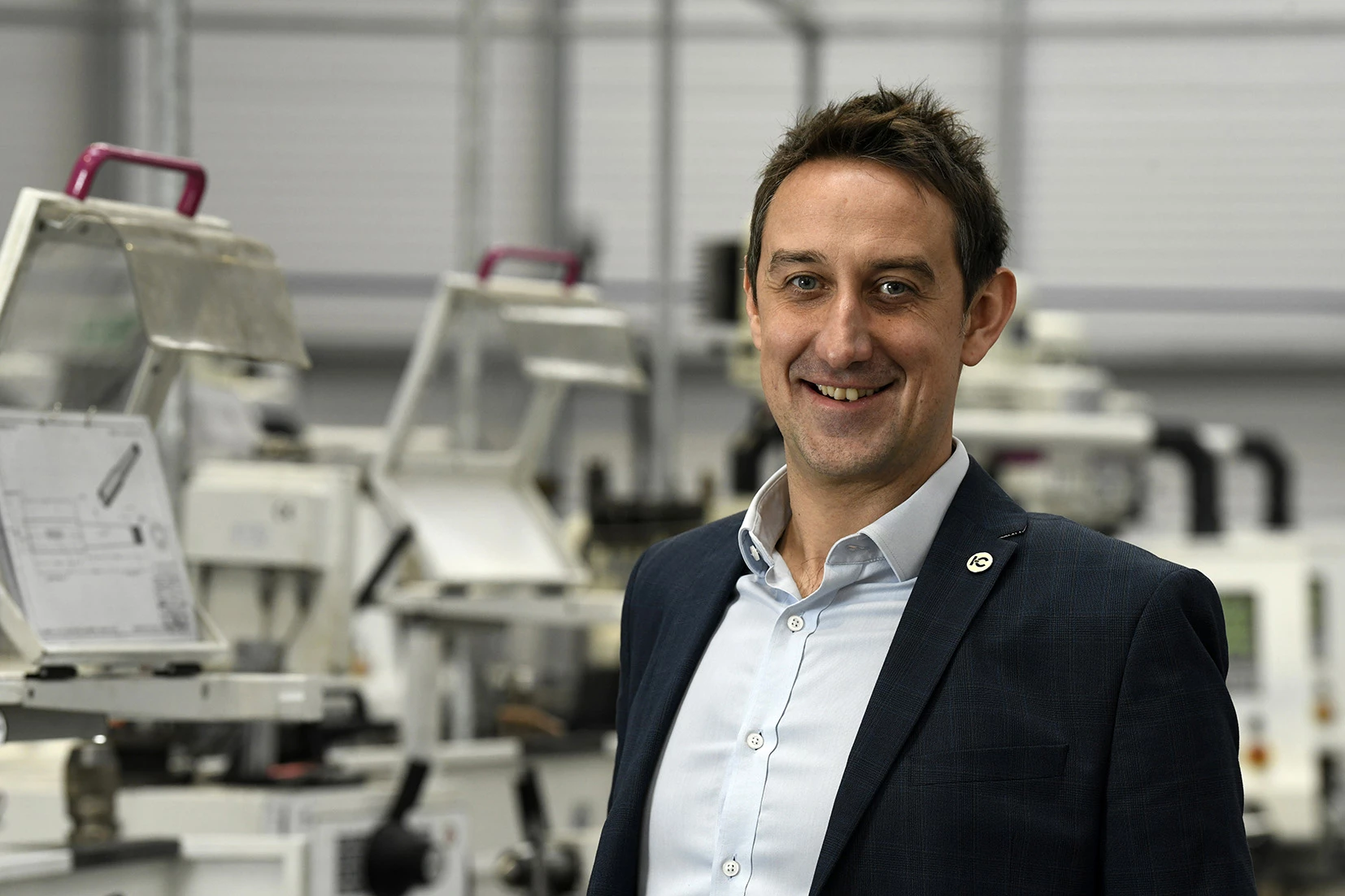
Partner Article
Report reveals a lack of skills is holding back the UK’s big reshoring drive
More than half of manufacturers in the UK feel they don’t have the right skills to take advantage of the growing ‘reshoring’ trend according to the In-Comm Training Barometer out today.
53% of companies said they would need to invest in boosting the skills of the workforce if they are to bring work home, with just over a quarter saying they have successfully brought contracts back over the last twelve months.
A similar number (23%) have kickstarted reshoring strategies, with the majority holding back due to restraints with their current and future workforce.
The findings, which covered more than 100 manufacturers, hammered home the current labour shortage hitting industry and indicated changing perceptions towards ‘growing your own’ staff.
On a positive note, 82% of management teams have indicated they are planning to take on an apprentice in the next twelve months, citing developing future talent as the most popular reason followed closely by ‘filling a skills gap’.
Just 12% said the latter was their reason for investing in vocational learning in 2022, compared to 46% this time around, highlighting what could be a real shift in how firms are taking a longer-term approach to overcoming ‘people’ shortages.
It appears industry has woken up to the fact that it needs to develop its own talent pools as outbidding rivals for staff is only going to be a short-term fix.
“It’s a very complicated training and skills landscape out there at the moment,” admitted Gareth Jones, Managing Director of In-Comm Training, which runs two state-of-the-art Technical Academies in Aldridge and Telford.
“Engineering and manufacturing seem very buoyant and we’re constantly hearing stories of growth and new opportunities, especially around future mobility and a resurgent aerospace sector. Our Barometer echoes this in part, but also paints a picture of a sector that is massively hamstrung by a lack of skills.
“An already huge gap has been accentuated due to Brexit and effects of the pandemic, not to mention the fact that businesses are fishing in a jobs market that is favouring the candidate more than the employer for the first time in years.”
He continued: “So how are manufacturers responding? This is where things get very complicated.”
Although more than three quarters are worried about retirement causing an even bigger drain on skills, this is not directly reflected in the number of firms planning to upskill their existing workforce to fill some of the gaps that are appearing.
Only 55% of companies plan to boost the skills of their existing staff, a figure expected to be much higher considering the lack of ready-made options and the benefits of flexible upskilling courses that give the ability to boost the skills of the workforce whilst minimising disruption to production.
Gareth went on to add: “This is where we need to engage the disengaged businesses. There are too many owner-managed companies not looking to grow or develop succession plans, resulting in some really good manufacturers failing due to a lack of planning.
“One of the barriers is often losing staff for a significant length of time when they are training, which leads me to think we need to explore more modular, shorter courses rather than longer, wider qualifications. Firms want employees that have a specific skill set and that sometimes doesn’t fit an apprentice framework for example.
“In reality, industry wants the old EITB model back where it becomes a levy for all types of training and not just for apprenticeships. We’re certain that would be the holy grail for employers.”
Whilst a lot of the skills issues for manufacturers have been long running, the next industrial revolution has developed the need for a new set of skills, predominantly around Industry 4.0 and Digital Manufacturing.
These were identified in this year’s In-Comm Training barometer as being key requirements, with 48% and 54% respectively saying they want to invest in these areas. They have also risen in importance from 2022, whereas electrification has remained constant, hovering around the 20% of respondents mark.
Gareth concluded: “I believe this trend can be directly attributed to how more and more manufacturers are engaged in data capture and digital transformation projects, meaning there is an immediate need for skills to support these efforts.
“The potential for electrification is huge, but maybe we are yet to see it permeate down all tiers of the supply chain? These figures tend to reinforce that notion.”
All the intelligence generated from the In-Comm Training Barometer will be shared with key industry stakeholders, technical partners and with Ministers to accelerate positive change when it comes to future skills funding.
The findings are also used to support industry, and this could be through the delivery of more modular programmes (both inside and outside of conventional working hours) and by creating more unique offerings like the recently launched Precision Tooling Academy with Brandauer.
For further information or to download the report, please visit https://in-comm.co.uk/training-barometer/ or follow @incomm_training on twitter.
This was posted in Bdaily's Members' News section by Russ Cockburn .
Enjoy the read? Get Bdaily delivered.
Sign up to receive our popular morning National email for free.