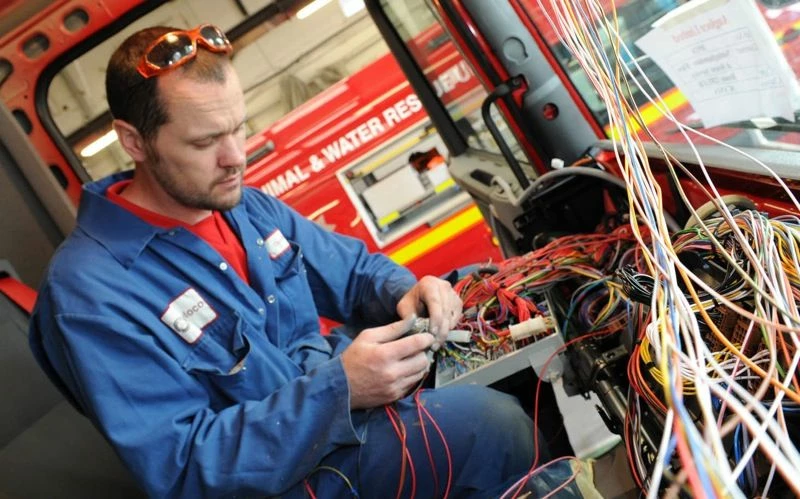
Partner Article
Rapid response to lean boosts West Yorkshire fire fighting specialist
A £17m turnover West Yorkshire manufacturer that supplies into more than 50 countries across the world is targeting further growth after tapping into support from the Manufacturing Advisory Service (MAS).
Angloco, which designs and manufacturers fire fighting and rescue vehicles, has smashed the £17m annual sales barrier for the first time in its 45-year history after embracing the principles of lean to speed up production and increase capacity.
The company called in MAS to help it improve efficiencies and build time at its impressive Station Road facility in Batley and, following extensive operator training, reviews of manufacturing flow and the implementation of best practice systems, it is now producing vehicles one month quicker than before.
This means the firm will be able to meet growing demand from its clients, which includes customers as far away as Zimbabwe and Afghanistan.
Kevin Sedgwick, production director, said: “A lot our work is custom made and we have a wide array of different models that serve industry, aviation and local authorities.
He continued: “This can put a lot of pressure on the shopfloor and in particular how we can best maximise the skills of the workforce to ensure we maintain quality whilst also speeding up the build process.
“We knew many of the changes that we wanted to make and MAS helped facilitate this by ensuring complete workforce buy-in and that lean manufacturing principles were adhered to.”
Angloco, which employs 65 people, introduced better control of the pre-build design review, with production owning this process and providing a greater input into engineering design.
It was agreed not to start vehicle build until there was design confirmation and build materials available then progress would be uninterrupted. Only one vehicle per bay would be worked on at any given time.
This generated space to allow line side delivery of parts to the job, making available materials visible and reducing individual trips to stores. Angloco introduced a standard bench and racking system developed for each bay, whilst consumable items were replenished on a kanban basis.
Finally, a status board and daily start of shift meeting was introduced to co-ordinate activity to support efficient production.
MAS’ Stephen Gregory added his support: “Angloco’s entire operations team took on board the continuous improvement journey and implemented changes, which transformed the supply of information, workshop organisation and material control over a very short period of time.”
Angloco is hoping to add to its existing turnover this year as it continues to aggressively target new markets and opportunities. If successful, this could lead to the creation of new jobs in West Yorkshire.
This was posted in Bdaily's Members' News section by Mark Lane .
Enjoy the read? Get Bdaily delivered.
Sign up to receive our popular Yorkshire & The Humber morning email for free.