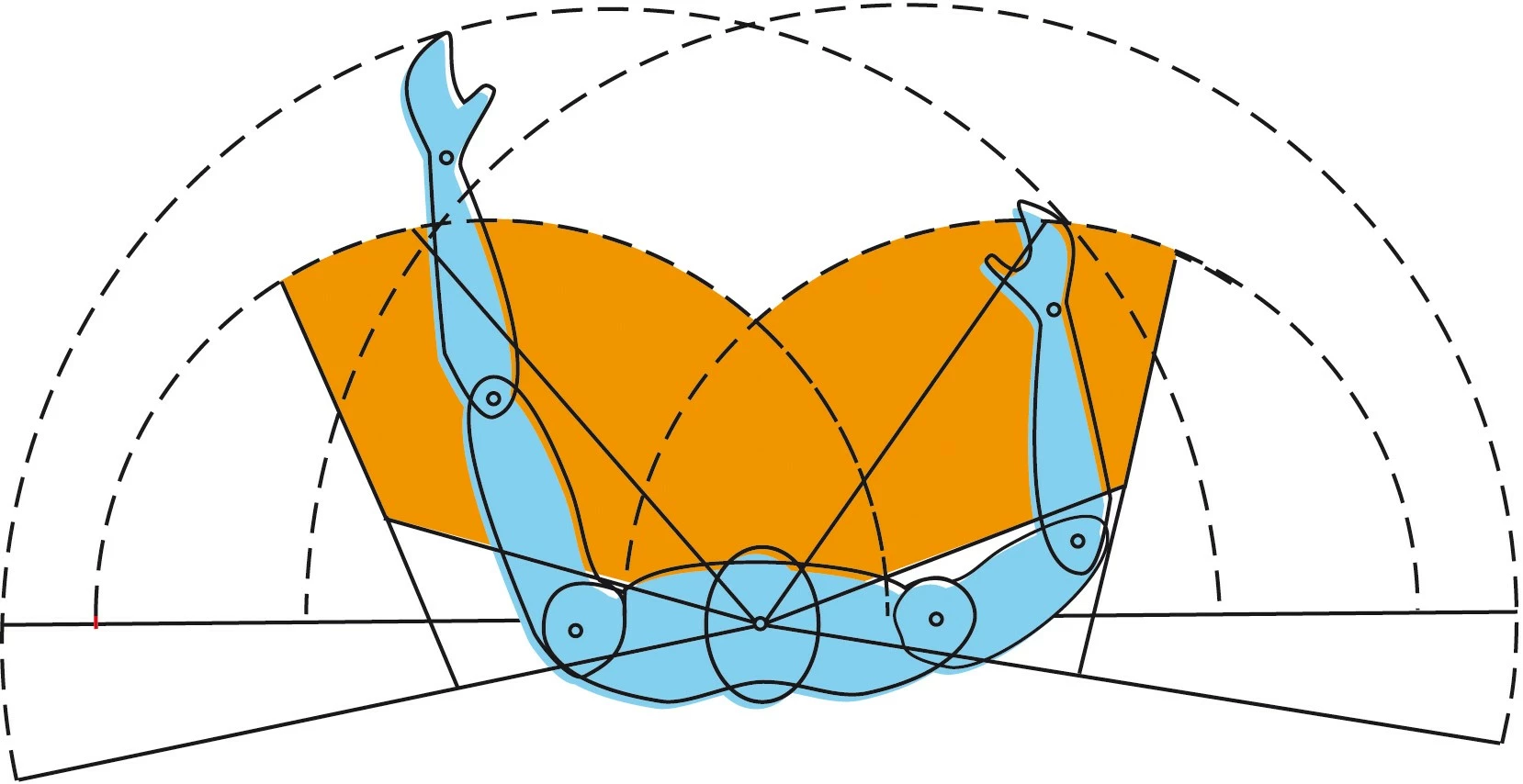
Partner Article
Helping you to reduce workplace injury claims ….. as well as improving operator efficiency.
By assessing people’s abilities and limitations, their jobs, equipment and working environment as well as the interaction between them, it is possible to design safe, effective and productive work systems. Business Transformation Associates Ltd. (BTA) offer a service to their clients that focuses on operator care.
Workstation Ergonomics is a science concerned with the ‘fit’ between people and their work. It puts people first, taking account of their capabilities and limitations. Ergonomics aims to make sure that tasks, equipment, information and the environment fit each worker and can reduce the potential for ill health at work, such as aches, pains and damage to the wrists, shoulders and back.
Kim English, BTA Director, stated “The Health and Safety Executive (HSE) estimate that there were 159,000 new cases of musculoskeletal injuries in 2016/17; making it the most common self-reported work-related illness category, with numerous musculoskeletal injury compensation claims being filed against employers each year”. Kim went on to say “BTA are in the business of helping our clients improve operating costs and cost avoidance naturally forms part of our commitment to deliver business efficiency improvement”.
Good ergonomic design and top level commitment to the principles of ergonomics will ensure your workforce performs at an optimal level with minimum risk of errors, incidents and personal damage. Ergonomics helps people work better and, if applied correctly, can increase efficiency and productivity, as well as levels of safety and health.
Colin Hastings, Company Director, told us “To assess the fit between a person and their work, you have to consider a range of factors. Our audits and assessments go beyond the conventional compliance-based risk assessment. Our extensive rating system considers 22 bodily movements, or activities as they are more commonly known e.g. bending, twisting, stretching etc. and the time spent and effort involved with each. The main emphasis of our analysis is on the amount of physical effort an operator needs to exert in order to fulfil a work assignment. The data generated will guide us to provide our clients with a focused and useful scope of work”.
BTA’s Operator Care Programme is aimed at providing clients with an additional service to support a well-managed safe working environment for all its employees. BTA can audit as an independent third party or contribute to a site team, supporting an existing health and safety management system. During these times of increasing industrial injury claims it is certainly worth investigating how an operator care programme can not only compliment your risk assessment process, but also potentially save your company the avoidable expense associated with lost time working, injury investigations, medical examinations, solicitors’ fees and compensation, as well as any unwelcomed publicity.
This was posted in Bdaily's Members' News section by Business Transformation Associates Ltd. .
Enjoy the read? Get Bdaily delivered.
Sign up to receive our popular morning National email for free.